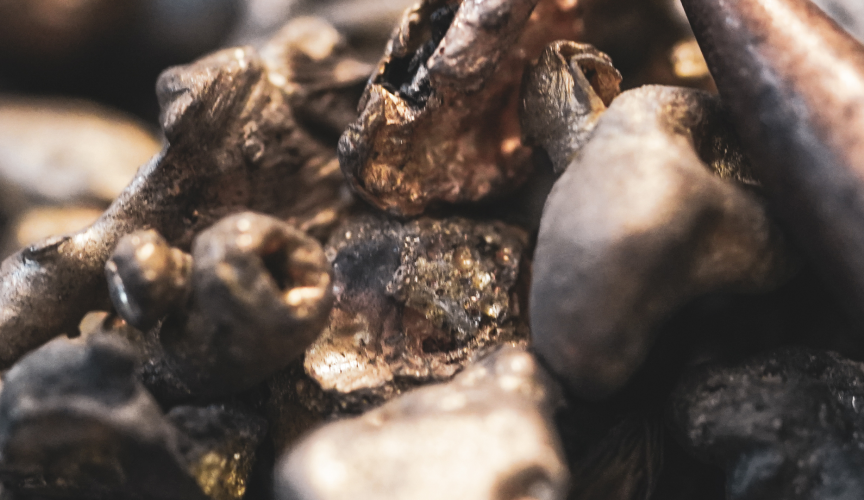
Every ton of municipal solid waste (MSW) burned in a Waste-to-Energy (WtE) plant contains valuable hidden resources, chief among them: metals.
Incinerator Bottom Ash (IBA) is rich in ferrous, non-ferrous, and precious metals. Yet, depending on how this ash is handled, these resources may be recovered or lost forever.
Metal Recovery: Economic and Environmental Value
Recovering metals from IBA delivers a compelling dual benefit - economic return and environmental sustainability.
ECONOMIC REVENUE
IBA typically contains between 10–15% recoverable metal content by weight, comprising:
- Ferrous metals: 7–10% (iron, steel)
- Non-ferrous metals: 3–5% (aluminum, copper, zinc, brass, stainless steel)
- Precious metals (in trace amounts): gold, silver, palladium—especially in e-waste-rich municipal streams (Source: CEWEP, 2020; Eurostat, 2022)
This translates to a global metal recovery potential of 4–6 million tons annually from the estimated 40–50 million tons/year of IBA generated by WtE plants worldwide (Source: ISWA, 2020; BDSV, 2023).
Depending on throughput, metal mix, and local market prices, recovered metals can generate:
- €10–30 per ton of MSW incinerated
- €1–6 million per year for a medium-size WtE plant (200,000 t/year capacity)
(Source: UrbanMine, 2021; UK Waste & Resources Action Programme - WRAP, 2018)
Dry-recovered metals - especially fine non-ferrous particles—fetch higher market prices due to reduced oxidation and moisture content, further boosting revenues.
SIGNIFICANT CARBON SAVINGS VERSUS VIRGIN EXTRACTION
Metal recycling from IBA drastically reduces the environmental burden of raw material extraction.
Recycling 1 ton of steel saves ~1.5 tons of CO₂-eq and 1.4 tons of iron ore (World Steel Association, 2021) while recycling 1 ton of aluminum avoids up to 9 tons of CO₂-eq emissions and uses 95% less energy than producing aluminum from bauxite (U.S. Environmental Protection Agency, 2016; European Aluminium Association, 2020).
Given that WtE plants worldwide produce an estimated 40–50 million tons of IBA annually, if just 50% of the recoverable metals were recycled, it could prevent 20–30 million tons of CO₂ emissions annually - equivalent to removing 6–9 million passenger cars from the road each year (European Environment Agency, 2021).
Why Wet Systems Fall Short
In traditional wet ash handling systems, hot IBA is quenched with water, leading to:
- METAL OXIDATION - Contact with water at high temperatures accelerates oxidation, particularly in non-ferrous and fine metal particles, reducing both yield and recyclability.
- AGGLOMERATION & SLAGGING - Ash particles tend to fuse or clump together, making screening- or density-based separation less effective.
- LOSS OF FINES - Lightweight non-ferrous metals like aluminum and zinc are lost in the fine fractions or washed out.
- DILUTION AND CONTAMINATION - Water exposure introduces impurities (e.g., chlorides), further degrading material quality and increasing post-treatment needs.
The result? Lower yields, reduced purity, and lower market value.
The Dry Advantage: How MADAM maximizes metal recovery
Dry IBA management paves the way for cleaner, more efficient, and higher-yield metal recovery, transforming residual ash into a veritable urban mine.
Leading this transformation is MADAM (MAgaldi Dry Ash Management), a fully dry system that eliminates the pitfalls of traditional wet handling. By keeping IBA dry throughout the entire handling process, from boiler discharge through to metal separation, MADAM preserves the physical and chemical integrity of metals, creating ideal conditions for efficient recovery.
The system seamlessly combines dry extraction, air cooling, and mechanical ash handling with targeted treatment of dry IBA. This process delivers an ash matrix perfectly suited for advanced sorting technologies, including magnetic separators for ferrous metals and eddy current separators for non-ferrous particles— tapping into the hidden value of IBA.
Key benefits include:
- HIGHER RECOVERY RATES
The dry state of IBA - thus the absence of agglomeration - enables the recovery of fine fractions down to 0.2mm, typically lost in wet systems. This reduces at the same time the pollution of fine heavy metals during the utilization or landfilling of the treated IBA aggregates afterward. - HIGHER PURITY (NO OXIDATION)
Air cooling prevents oxidation, preserving the surface conductivity and bonding characteristics of non-ferrous metals. With fewer contaminants, recovered metals can be directly routed to refining or recycling facilities, commanding higher market value. - INDIRECT CARBON SAVINGS
One of the most impactful—though less visible—benefits of dry IBA management is its role in indirect carbon savings. Recovered metals are not just an end-of-pipe benefit: they close the loop in material cycles. When extracted efficiently, these metals re-enter industrial value chains, displacing virgin raw materials and dramatically lowering lifecycle emissions. According to the European Environment Agency, recycling a single ton of aluminum can prevent up to 9 tons of CO₂ equivalent, while recycling steel saves approximately 1.5 tons of CO₂ per ton.
Conclusion
In modern waste management ecosystems, metal recovery is no longer an optional add-on.
Regions with advanced circular economy policies, like the European Union, already recognize this importance. The European Commission’s BREF on Waste Incineration (BAT Reference Document, 2019) lists dry bottom ash treatment and metal recovery as Best Available Techniques (BATs) under the Industrial Emissions Directive (IED), underscoring their compliance-driven and future-ready nature.
Implementing dry IBA management systems - like Magaldi’s MADAM - goes beyond environmental compliance, delivering:
- Revenue diversification for WtE plant operators
- Reduced lifecycle emissions across the waste and metal sectors
- Enhanced circularity and resource sovereignty at a national level
- Alignment with ESG goals for investors and municipalities.
As the pressure to decarbonize intensifies and raw material supply chains become more vulnerable, the metals hidden in bottom ash represent both an economic opportunity and a strategic imperative.