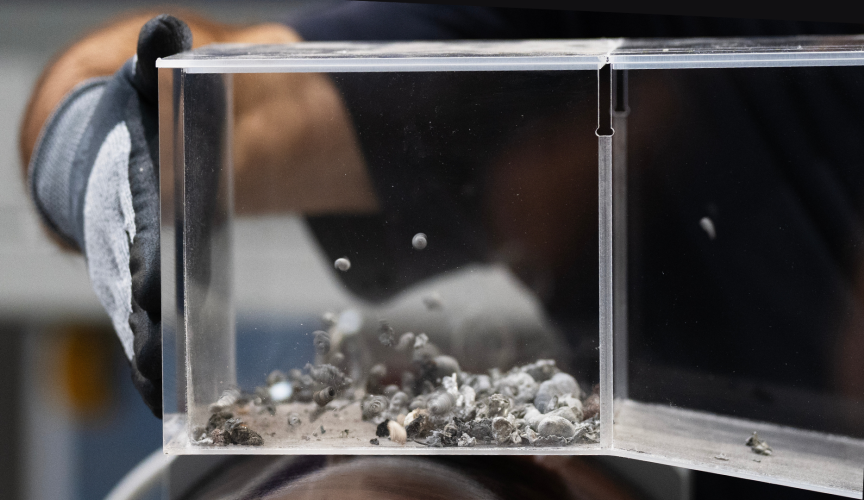
Industry data suggest that every ton of Incinerator Bottom Ash (IBA) can contain up to 10-15% recoverable metals - a potential goldmine, both economically and environmentally.
Yet, despite this potential, many Waste-to-Energy decision-makers hesitate to invest in full-scale IBA treatment systems. Why? Because the decision isn’t straightforward. It hinges on volatile metal market prices, fluctuating landfill fees, complex permitting landscapes, and, most critically, uncertainty about what is actually in the ash. Perceived or actual inconsistency in metal content stalls progress and investment. That’s where Magaldi comes in!
The Magaldi Ash Insight Unit: Bridging the Gap
At Magaldi, we understand that investing in IBA treatment isn’t just a technical decision but a strategic move. That’s why, to bridge the gap between potential and action, Magaldi has developed the Mobile Test Facility, an Ash Insight Unit that enables on-site analysis of the ash generated under real operating conditions, empowering WtE operators with actionable insights that support both technical and strategic decision-making.
Designed for deployment directly at the WtE plant, the unit eliminates the need to ship samples across borders, navigate delays, and wait weeks for results that may not reflect actual on-site conditions.
What does it test?
The Magaldi Mobile Test Facility replicates critical equipment of a full-scale dry IBA treatment system, making it an essential diagnostic and planning tool. Key parameters include:
- NON-FERROUS METAL RECOVERY (0.2–20 mm) through an onboard eddy current separator — replicating full-scale dry IBA treatment capabilities. As 70–80% of IBA revenue potential lies in fine non-ferrous particles, this analysis is central to project feasibility.
- ESTIMATED FERROUS METAL CONTENT evaluated via magnetic separation.
- PARTICLE SIZE DISTRIBUTION, determination of magnetic fractions, and separation capabilities for future equipment — all critical for system design, equipment sizing, and economic forecasting.
How does it work?
The Mobile Test Facility follows a structured methodology that ensures accuracy, repeatability, and relevance:
- STEP 1: CUSTOMIZED SAMPLING STRATEGY
Magaldi’s engineering team visits the WtE site to co-develop a tailored sampling plan. This strategy is adapted to the plant’s operational layout, waste stream variability, and specific IBA valorization strategy. This ensures the process is safe, representative, and fully aligned with site-specific constraints. - STEP 2: SAMPLING OVER TIME
To capture the inherent variability of municipal solid waste (MSW), ash samples are collected over several days. This approach avoids the limitations of single-day testing and results in a robust, statistically valid dataset. - STEP 3: IMMEDIATE SAMPLE DRYING
Collected ash samples are promptly dried to prevent oxidation, minimize contamination, and avoid loss of light particles. This step replicates the dry conditions of Magaldi’s dry ash handling system, ensuring no metal degradation due to quenching or moisture. - STEP 4: ON-SITE METAL SEPARATION AND ANALYSIS
Within a day, the Ash Insight Unit is up and running. Onboard equipment includes magnetic separators for ferrous metals and eddy current separators for non-ferrous metals. The setup provides a real-time snapshot of the ash's composition and metal recovery potential.
What Information Does It Provide?
The Mobile Test Facility delivers a comprehensive set of performance metrics that form the foundation for technical and economic feasibility studies:
- Metal yield data quantifies the economic potential of resource recovery
- Particle size distribution supports the design of the large-scale IBA treatment system
These insights form the technical fundamentals for developing pilot systems, securing funding, and designing full-scale project designs, replacing assumptions with accurate, project-specific data.
From Pilot to Plant: Scalable by Design
Magaldi’s approach is simple: Start small, scale smart.
The MADAM system is designed for progressive implementation based on budget, capacity, and plant layout, rather than requiring a single large-scale investment.
Once the Mobile Test Facility confirms feasibility, Magaldi supports the next phases with:
- Pilot-scale implementation focused on recovering the most valuable ash fractions.
- Stepwise expansion of treatment capacity toward a full-scale, tailor-made MADAM deployment, aligned with the plant’s ash volume, composition, and strategic objectives.
Because the Mobile Test Facility simulates core functions of the MADAM system, transitioning from testing to deployment is seamless. This continuity reduces design redundancy, accelerates commissioning, and minimizes CAPEX risk.
Conclusions
Recovering valuable metals from IBA represents a strategic opportunity for WtE facilities. However, success requires more than ambition; it demands accurate, site-specific data and a scalable solution framework.
Magaldi’s integrated approach—combining real-time analysis through the Mobile Test Facility with the modular scalability of the MADAM system—allows operators to move forward with clarity and control. From feasibility to implementation, every step is grounded in measurable insight.
Because smart investment begins with real data. And real data begins by seeing through the ash.