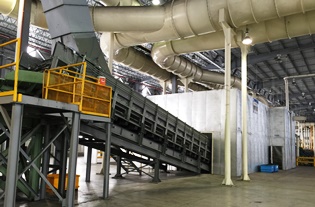
THE CHALLENGE
Recognizing the increasing importance of the Mexican automotive industry, Metal Technologies, Inc. (MTI) decided to invest in a greenfield foundry in San Luis Potosí to produce almost 100,000 tons per year of gray iron castings.
In 2015, MTI entrusted the engineering and project management to GEMCO Engineers BV which will deliver the project turnkey including installation and commissioning.
In 2017, Magaldi was awarded with a contract to supply its dependable technologies, providing:
- an enhanced version of the MCC® (Magaldi Casting Cooler) – known as SuperMCC® - for cooling and conveying castings and sprues;
- a Magaldi Spill Chain to be installed underneath the SuperMCC® for sand return conveying;
- a Magaldi Superbelt® for sprues conveying;
- a Magaldi Superbelt® conveyor for casting sorting after shot blasting.
THE CUSTOMER
Based in Auburn, Indiana, Metal Technologies Inc. (MTI) is a leading metal casting company dedicated to providing customers with over 300,000 tons per year of the highest quality gray, ductile, austempered iron and aluminum castings for a variety of industries.
MTI operates multiple manufacturing facilities in Indiana, Michigan, Minnesota and Tennessee. Its operations include four iron foundries, two aluminum die-casting plants and a tooling, gaging and machining company.
Recently, MTI decided to establish its manufacturing capabilities in Mexico, building a new ductile and gray iron foundry which will be located in San Luis Potosí.
THE SOLUTION
Produced on a vertical green sand molding line, castings will fed the SuperMCC® by means of a vibrating shake-out conveyor.
The SuperMCC® is designed to cool down the castings in a 23 m cooling tunnel, from an initial temperature of 600 °C to a final surface temperature ≤100 °C through an optimized cooling process.
This enhanced process guarantees improved performance thanks to both co-current / counter-current and cross-flow heat exchange mechanisms among the castings and a forced cooling air flow.
The cooling tunnel is equipped with two cold cooling air inlet points placed at the tunnel ends and with a hot air suction point at the middle of the same.
The SuperMCC® is provided with the MISS® (Magaldi Integrated Supervision System) to control equipment operations. Optical pyrometers are installed in pairs respectively at the entrance, at the middle and at the exit of the cooling tunnel, to detect castings temperature along the transportation. Relevant signals will be available to the MISS® in order to adjust, if necessary, inlet and/or outlet air flow rates, depending on detected castings temperature, and the SuperMCC® belt speed, depending on the casting type to be treated (ID code).
Although castings are separated from sand on the vibratory shake-out conveyor, there will still be residual sand on castings when entering the cooling conveyor. For this reason, a Magaldi Spill Chain has been installed underneath the SuperMCC® for sand return conveying.
Once cooled down, castings will be discharged onto a reversible vibrating conveyor, installed perpendicular to the conveying direction of the SuperMCC®. Castings and sprue will be separated and then sprues will be discharged onto the Superbelt® conveyor.
Designed with upstanding side walls to reliably handle sharp materials and to avoid spillage from remaining sand and metal parts, the Magaldi Superbelt® will convey sprue and reject castings from the shotblasting area to outside.
Magaldi also supplied a further Superbelt® conveyor for de-gating activities.
After shotblasting, castings will be discharged onto a Superbelt® conveyor with downfacing side walls to easily slide castings off the belt. Several operators will work alongside the conveyor taking-off castings for grinding and inspection.