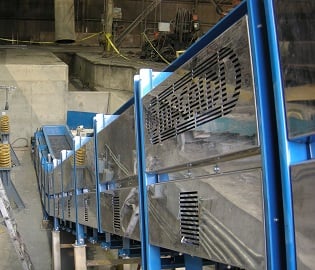
THE CHALLENGE
A U.S. foundry selected Magaldi Technologies as equipment provider for a new sand infeed conveyor.
The existing vibratory conveyor handles green sand which is separated from castings and sprues via a manipulator, while molds are being transported on a shake-out conveyor. Sand from the shake-out is conveyed at a 90° angle and dropped into the lower infeed conveyor. Sand is eventually discharged into a rotary drum, where the big chunks are broken, and tramp metal recovered before sand reclamation.
The existing infeed conveyor is badly worn-out, requires high maintenance costs to keep it running, and continuously spreads sand in the surrounding environment. That’s why the foundry management opted for a change of technology, selecting the Magaldi conveyor to improve operations and cleanness of the area.
THE SOLUTION
In close cooperation with the Customer, Magaldi has been able to design a solution to fit in the same space occupied by the vibratory infeed conveyor, with only minor modifications to the existing structures.
The Superbelt® will gently convey the sand discharged from the shake-out, and any residual metal tramp, up to the drum, solving all operational problems caused by the existing vibratory infeed conveyor. Installed HP will be lowered by 70%, silica emissions will be drastically reduced, and O&M costs will be offset thanks to the special design of the belt which ensures long-lasting life span.
“We have been searching for some time for a cost-effective, high-value, conveying technology for our sand transfer conveyor. In Magaldi we have found a partner who can deliver the performances we require” stated the Maintenance Manager, who led the due diligence process.
The Superbelt® conveyor will be in operation by the third quarter of 2021.
BENEFITS
- Low noise level (<80 dB(A))
- Minimal silica dust generation during sand transfer
- Lower power demand: 70% reduction
- Long belt life expectancy (10 to 15 years)
- Minimum operational and maintenance costs
- Little to no foundation required (no dynamic load) and installation in the same footprint of the vibratory conveyor