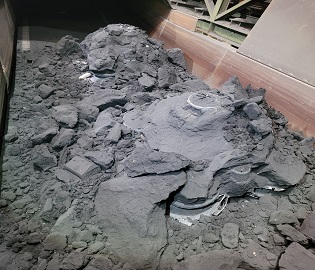
THE CUSTOMER
Founded in 1905, Hermann Reckers GmbH & Co. KG is a well-known iron foundry, manufacturer of complex castings and components for hydraulic, pump housing and valve constructions, located in Rheine, West Germany.
THE CHALLENGE
The molds, poured along the horizontal molding line, were transferred from the punch-out area to the shake-out area by means of two rubber belt conveyors (one in operation and the other one 100% in stand-by). From the outset, the spare conveyor had been necessary to secure the production in case of failure or repair of the other conveyor. Additionally, the rubber belt conveyors suffered from frequent damages caused by hot temperatures encountered during operation.
To reduce the high maintenance costs, Hermann Reckers foundry chose to replace the existing conveyors with a Magaldi Superbelt®, whose damage-tolerant design guarantees higher dependability.
THE SOLUTION
The Superbelt® conveyor is 24 meters in length and 800 mm in width, with an inclination of 2 degrees. To keep fumes emission under control, the conveyor will be equipped with top covers and three suction hoods connected to a de-dusting system.
The installation is scheduled for July 2021 during the planned line outage.
The Superbelt® conveyor will allow to easily and softly convey the molds without any dust spillage into the surrounding environment.
BENEFITS:
- High temperature resistance
- Extreme wear and abrasion resistance
- Gentle motion without vibrations
- Low power consumption
- No need to use heaters to heat the surface of the trough. Sand sticking and build-up issues overcome.