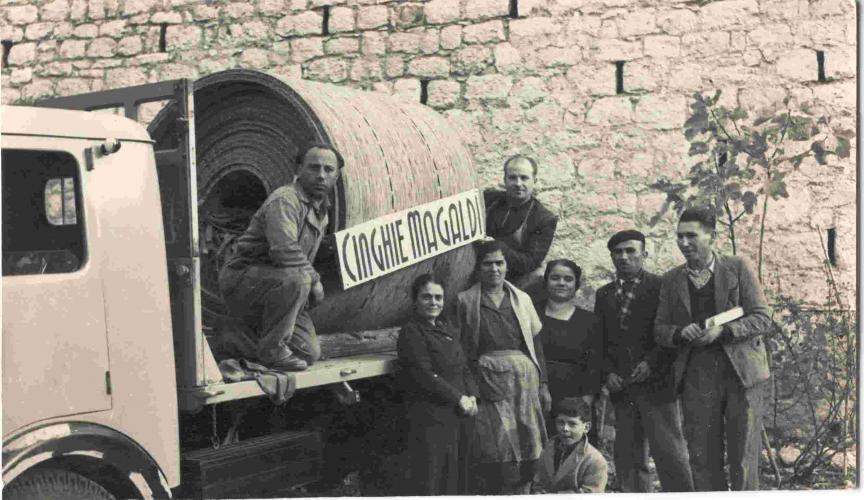
Remaining true to its fundamental values but constantly innovating, Magaldi succeeded in establishing itself as internationally recognized technology leader. To stay at the forefront of the business, the firm continuously develops its proprietary technologies thanks to the efforts of its in-house R&D team. that, since the Supercinghia, has developed a broad range of solutions to handle virtually all materials and debuted in the renewables market with a breakthrough Concentrated Solar Power technology.
MAGALDI INVESTS IN R&D TO DRIVE INNOVATION AND DEPENDABILITY
Since 1929, innovation and dependability are the cornerstone on which Magaldi has built its success
story. A long-standing tradition of innovation and knowledge has consolidated its global footprint and made the company a preferred technology partner that enjoys the trust of a wide range of customers worldwide. Right from our customers, the innovation process begins: we listen their wishes, make their challenges our own and draw on expertise and know-how of our inhouse R&D team to develop exciting solutions able to add value to any customer. Magaldi does not sell products, it provides dependable solutions. That is why we invest about 3% of our turnover in research and innovation every year, in order to continuously confirm and expand our technological pioneering role and to turn ideas into viable technologies. In fact, innovating is more than inventing: we strive to ensure our customers could see the commercial value in our solutions, getting benefits higher than their cost. Since the first invention - the Magaldi Supercinghia - from which the whole story of the company originated, more than 20 patents for proprietary technologies have been registered, generating approximately 400 patent applications worldwide. Dependability is the other cornerstone of Magaldi entrepreneurial philosophy.
It sums up:
- availability, as readiness for correct service. All Magaldi systems are developed to guarantee maximum availability and to perform around the clock;
- reliability, as continuity to run without sudden failures. The Superbelt® - core technology of all Magaldi solutions - has been conceived and designed to prevent any line shutdown, even if something breaks. Its construction features allow to continue running and to schedule maintenance according to production needs;
- maintainability. By developing new solutions or improving the existing ones, Magaldi does not neglect the aspect of maintainability. Even conveyors enclosed in steel casings are designed to allow operators to safely and comfortably maintain the system from outside. Moreover, all components are chosen to guarantee maximum resistance to wear and external stress, for a minimum requirement for spare parts;
- safety, for operators and for the environment. Magaldi cares about health and safety not only of its operators but also of those who will use its technologies. That’s why we develop solutions that contribute to a safer and healthier workplace environment, lowering the exposure of operators to harmful agents (e.g. crystalline silica sand) and possible accidents. Magaldi also continuously explores ways to do more for the environment. Its dry technologies developed for solid-fuel power plants have revolutionized the power sector and introduced a viable and eco-friendly solution, alternative to conventional polluting technologies. Designing technologies with dependability is our way to ensure their success.
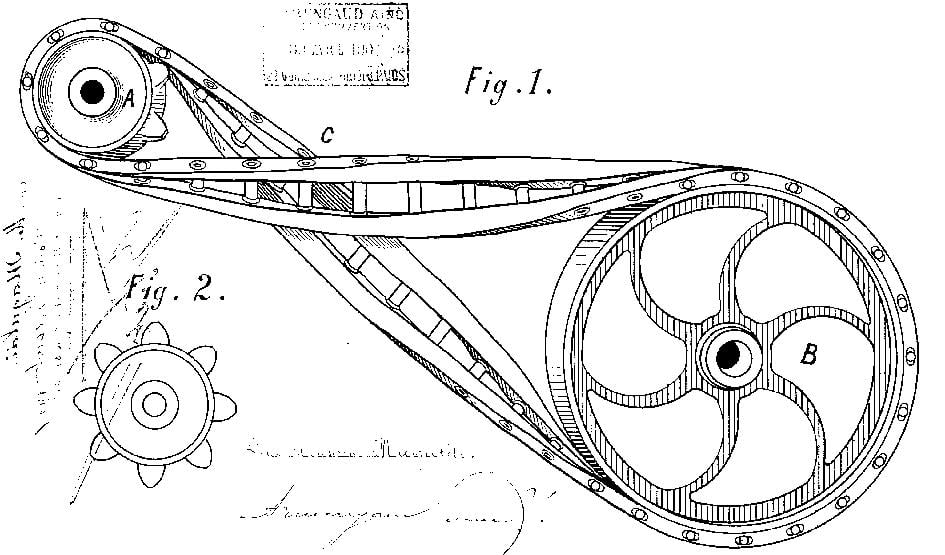
NINETY YEARS OF SUPERCINGHIA
At the beginning buffalo leathers, then leather strips tanned with chrome to increase their resistance, finally steel belt. Hence, the story of a company representing a successful example of that family capitalism that is the pride of the Italian entrepreneurship. Designed and patented by Emilio Magaldi in 1901 as power transmission belt, the Supercinghia marked the starting point of Magaldi’s entrepreneurial activity. In 1929, Paolo Magaldi turned the family workshop activity into an industrial business. Made of buffalo leather strips placed side by side and connected with metal rivets, the Supercinghia immediately penetrated the market thank to its extremely reliability and virtually indestructibility. The accidental breaking of a single strip did not spread to the entire width of the belt and did not require immediate replacement. On the contrary, belts made of wide strips of leather with joints placed very closely could suddenly break under stress in their weakest point, thus interrupting operations and posing hazards to workers. But inventiveness was not limited to develop new products. In 1930, Paolo patented a technique for cutting the buffalo leather skin in a spiral, so to produce a single strip 100-150 m long. In this way, there was no need for hundreds of joints required in previous productions, and the Supercinghia Magaldi was even more reliable. Magaldi perceived the potential of the Supercinghia and over time perfected it to become even more reliable, with the result of extending its area of application to many different business sectors, all facing the need to handle materials in severe process conditions. Thus, the Supercinghia evolved in the steel Superbelt® conveyor. Summing up dependability, quality and innovation, the Superbelt® is currently the jewel in Magaldi’s crown since it represents the core technology of all its systems. Nevertheless, the Supercinghia never lost market and it is still used today for steel sheets conveying in different applications (e.g. sheet metal stamping lines, cut-to-length lines, coil wrapping machines, etc.), providing higher reliability and a longer service life (more than 10 years!) when compared to conventional rubber or fabric conveyor belts. The Portuguese Volkswagen Autoeuropa, for example, is still benefitting from 8 Supercinghia, installed 17 years ago and used to reliably convey car doors and other automotive components. Likewise, in the Italian SidAstico SpA, a sheet cutting machine is equipped with the same Supercinghia installed 18 years ago and so many others installed all over the world.
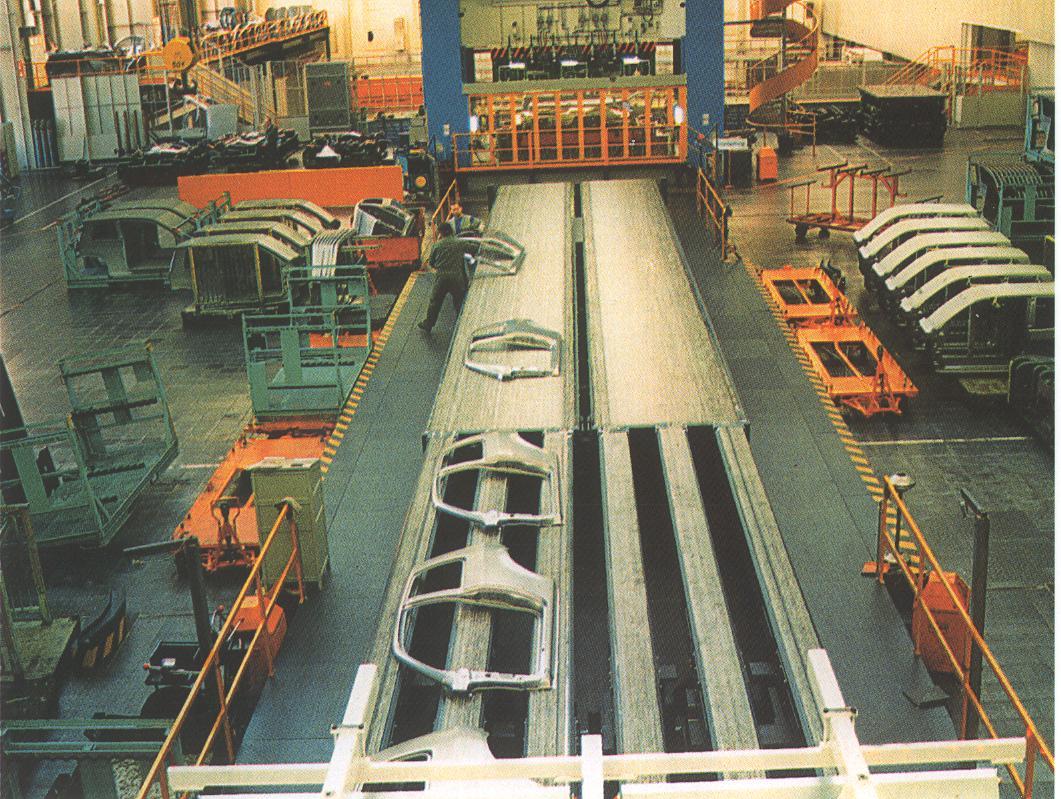