The Magaldi Casting Cooler
(MCC®)
A highly engineered system to efficiently manage the safe transport & controlled cooling of castings
One of the primary challenges in producing high-quality castings is the efficiency of the cooling process, which is affected by the casting resident time inside the cooling tunnel.
The cooling time can vary based on production volumes, casting size, available space, and other unpredictable factors. Thus, having a flexible system that can control the cooling process and adjust to specific production needs is crucial for success.
The MCC® is typically installed between the shakeout and the blasting machine. It consists of:
- The Superbelt® conveyor as the key component: The belt design is based on a multi-link concept, which ensures redundancy, requires little to no maintenance, and enables trouble-free continuous operation, thus avoiding costly disruptions.
- A cooling tunnel held under negative pressure: Ambient air is pulled through the extremities of the cooling tunnel and exits through the central hood. The controlled-speed cooling air flows over the castings, cooling them to the desired temperature without causing thermal shocks or other microstructural defects.
Rugged design
Casting cooling conveyors need to work in tough conditions, dealing with abrasive sand and castings, as well as extreme temperatures. To handle these challenges, heavy-duty machines are required.
The MCC® conveyor is known for its high resistance to abrasion even at high operating temperatures. The unique way the pans are connected to the mesh belt allows all components to expand in any direction without permanent damage, while the take-up device automatically compensates for thermal expansions.
Engineered cooling process
For every project, Magaldi meticulously investigates the thermal properties of both air and castings to deliver the most efficient cooling process. The combined use of analytical methods (CFD analysis), experimental tests on the in-house built test rig, and in-field measurements results in highly accurate thermodynamic models. This ensures effective modeling and, ultimately, the cooling process.
Controlled air-cooling
One of the most critical factors in the casting cooling process is the heat exchange method adopted to cool castings.
The MCC® conveyor uses in combination co-current and counter-current airflows. The result is a smaller temperature gradient at the inlet of the cooling tunnel, so that thermal stress in castings is reduced while the overall efficiency of the cooling process is maximized.
Compact design suitable for installations with limited space
With the SuperMCC® conveyor, a third airflow (cross-flow) enters the system through specially designed slots on the belt pans. Since cooling air not only flows around the castings but also passes under and through them, more of the casting surface area is exposed, resulting in a more effective cooling process and minimizing the equipment’s footprint, which makes it a great solution in settings where space is limited.
Integrated Supervision System (MISS®)
A fine-tuning step and adjustment of casting cooling parameters are crucial to gaining a reliable and flexible process. That is why the MCC® conveyors can be completed with the Magaldi Integrated Supervision System (MISS®), which performs a dynamic control on the process parameters in accordance with the different types of castings to be handled.
Linked to the molding line operation signals, the MISS® receives the ID number of each casting along with the actual casting temperature. Dependent upon the above parameters, it automatically adjusts the belt speed and the cooling airflow rate, thus maximizing both plant productivity and cooling process efficiency.
Reduced silica dust emissions
The MCC®/SuperMCC® conveyors provide a competitive edge in dealing with a highly sensitive issue, namely workers' exposure to crystalline silica dust.
The simple operation of the Magaldi conveyor system ensures smooth running without vibrations which, in turn, minimizes dust emissions, contributing to a safer and healthier work environment.
Low power consumption
The Superbelt® conveyor allows for reduced power requirements (about one-tenth of vibratory conveyors or cooling drums). Its unique design avoids sliding friction among the moving parts, thus minimizing wear and energy consumption for conveying and cooling process.
"All in one":
cooling, degating & sorting
With the MCC®/SuperMCC®, the uncovered length of the belt downstream the cooling tunnel can be used as a workstation for casting degating and sorting, avoiding the need for additional equipment. The gentle and low-noise transport allows operators to sort castings comfortably. Additionally, the belt is so sturdy to withstand impact loads coming from the degating tools (e.g. hammers, hydraulic wedges, manipulators, robots)
Some successful stories
Slovenia
Casting cooling
Iron foundry
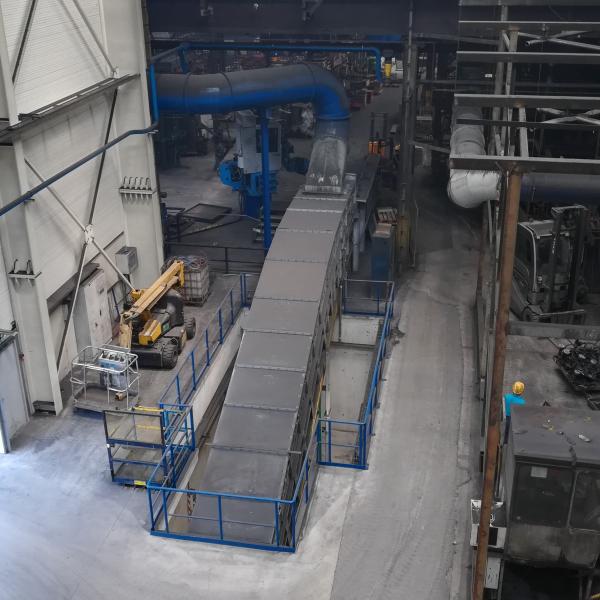
Optimal control of cooling parameters thanks to the MISS® system
The Customer
Leading manufacturer of ductile and grey iron components for the railway industry.
The Challenge
The target for the foundry was to cool huge and heavy castings featuring high temperatures and a high thermal module.
The Solution
Magaldi engineers conducted dedicated test rigs to validate the cooling curves obtained with proprietary simulation codes. The result was an MCC® conveyor able to cool the heavy (up to 633 kg) and large castings coming from the “L”-shape shake-out line from 700°C to 70°C.
Italy
Casting cooling
Iron foundry
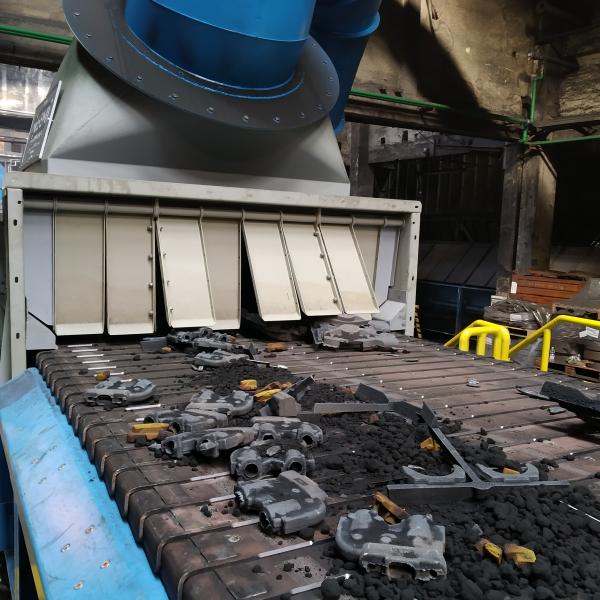
Engineered & controlled variable cooling process suitable for high volume production.
The Customer
The foundry produces grey and nodular cast iron for several industrial sectors.
The Challenge
As part of a project to modernize the DISA vertical lines, the Customer came to Magaldi looking for an integrated solution for casting cooling and degating while moving castings from the punchout to the shot-blasting machine.
The Solution
After the punch-out, 2 vibrating conveyors discharge castings on the MCC® placed orthogonally. The long MCC® cools castings according to the performance of the upstream DISA lines. At the exit of the cooling tunnel, casting sorting and degating is performed on the uncovered length of the belt. Gates fall into an automatic box handling system at the head section for onward transfer to the melting area.
P.R.C.
Casting cooling
Iron foundry

The MCC® was able to reduce scrap rates and maximize product quality through a customized air cooling process.
The Customer
Modern foundry dedicated to manufacturing cast iron cylinder blocks for the automotive industry.
The Challenge
The Customer reached out to Magaldi in search of a solution to improve the quality of its castings. The only way to reach this goal was by improving the performance and effectiveness of the casting cooling system.
The Solution
Downstream the shake-outs, 2 vibrating feeders collect and feed the MCC® conveyors, forming a single 54m-long tunnel where a continuous flow of 40 t/h of iron castings is cooled down from 450°C to 80°C. At the exit of the cooling tunnel, the uncovered length of the belt is used as a workstation to sort and degate castings by means of manipulators.