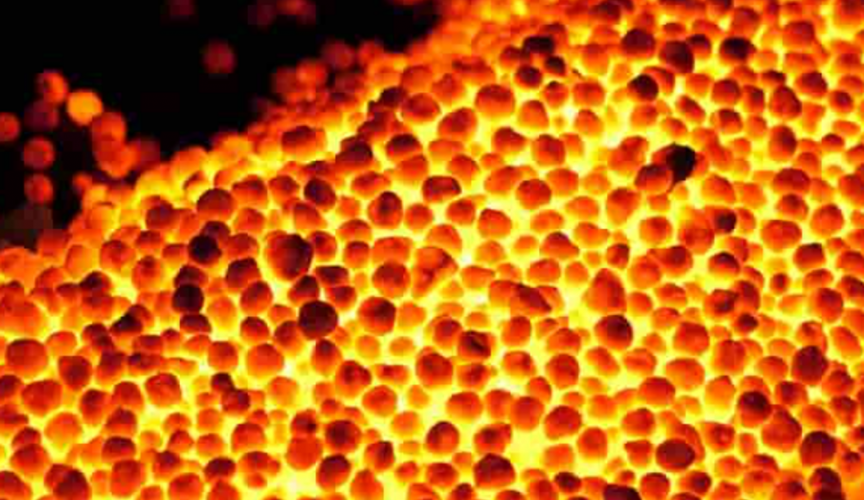
Achieving net-zero emissions in the steel industry requires bold innovation and fundamentally reshaping steelmaking processes.
The DRI-fed EAFs route is emerging as a promising solution for reducing emissions and meeting the growing demand for top-tier steel products.
Magaldi, leveraging its expertise in challenging, high-temperature applications, has developed a viable and environmentally sound alternative to traditional technologies for transporting hot DRI (HDRI) from the reactor discharge to the meltshop, capitalizing on the energy value of the HDRI in the EAF.
A sustainable future through the DRI-fed EAF route
While increasing the use of steel scrap can help decarbonize current crude-steel production routes, it falls short of a comprehensive solution. Steel demand continues to outstrip recycled supply, and available scrap may not meet industry standards. To bridge this gap sustainably, many steel companies are turning to DRI and electric melters.
Steel producers have two main options for integrating reduced iron into their processes: sending hot DRI directly to the EAF or feeding the melters with briquetted iron. However, briquettes require more energy per ton to melt compared to HDRI – about 100 to 150 additional kWh/tLS. Therefore, the integrated HDRI process stands out for its cost-efficiency and higher productivity. This suggests that an increase in DRI production is expected to be a key trend driving the growth of the global EAFs market.
The Ecobelt® DRI conveyor for integrated HDRI process
In recent years, reductions in CO2 emissions have come largely from the quest for more sustainable energy sources, primarily green hydrogen, to produce DRI. However, there are further opportunities for efficiency improvements connected to the DRI handling process.
Driven by its commitment to innovation and backed by extensive experience in handling hot materials under challenging conditions, Magaldi has developed a viable alternative to conventional technologies for transporting and charging HDRI.
The Ecobelt® DRI conveyor is the only fully enclosed conveyor of its kind for HDRI transportation from the direct reduction furnace to downstream processes, including the cooling station, briquetting machine, or EAF meltshop. Equipped with a thermally insulated cover, the conveyor system operates under an inert gas atmosphere that helps maintain the DRI's integrity during transportation while improving the downstream melting process and overall EAF productivity. In particular, the Ecobelt® DRI conveyor offers:
- HIGH DEPENDABILITY AND UPTIME
The redundant patented mesh system ensures continuous trouble-free transportation of HDRI, eliminating the risk of interruption or delay that could result in a loss of quality and efficiency for the entire plant.
- HIGH-TEMPERATURE RESISTANCE
Designed to withstand temperatures of up to 1100 °C (2,012 °F) without warping or deforming, the Ecobelt® DRI conveyor remains robust even when conveying DRI at temperatures ranging from 700 °C to 950 °C (1,292 °F to 1,742 °F). This eliminates the risk of equipment damage or costly process shutdowns due to hot spots in the DRI on the conveyor belt.
- LOW THERMAL DROP
With the Ecobelt® DRI conveyor, HDRI can be transported and charged to the EAF at up to 700 °C (1292 °F), capitalizing on sensible heat. Hot charging helps reduce the cost per ton of liquid steel by lowering power and electrode consumption, and tap-to-tap cycles while boosting EAF productivity.
- NO REOXIDATION AND EXTREMELY LOW NITROGEN REQUIREMENTS
The air seal provided by the full enclosure with an integrated inert gas system ensures that oxygen is kept out. This minimizes the risk of re-oxidation and preserves the high metallization level of the conveyed material, thereby enhancing product quality and energy efficiency. But what sets the Ecobelt® DRI apart from conventional technologies is its lower nitrogen injection along the conveyor: just one-third of the requirements of conventional technologies.
- EFFECTIVE DUST CONTAINMENT
Unlike pneumatic transport systems, the Ecobelt® DRI conveyor greatly reduces HDRI fines generation. The high velocity and resultant turbulence in pneumatic systems can cause significant breakage and erosion of the HDRI, resulting in fines generation of up to 8-10%. Moving slowly and smoothly, the Ecobelt® DRI conveyor overcomes such drawbacks while the full enclosure ensures that no dust is emitted from the conveyor and no spillage is generated underneath.
- LOW MAINTENANCE
Designed for low maintenance requirements, the Ecobelt® DRI conveyor is devoid of chains, wheels, or sprockets. Only the head and tail pulley bearings and return idler bearings require lubrication. The upper idlers and rollers are lubricated for life, and other elements are designed for continuous operation, allowing for preventive maintenance on a multi-year schedule.
- GREAT FLEXIBILITY
The Ecobelt® DRI is available as a pan plate or bucket conveyor to address challenging geometries of up to 75 degrees while transporting materials ranging from fine-grained to lumpy. This adaptability makes it suitable for various process requirements.
The Ecobelt® DRI conveyor represents a leap forward in sustainable steelmaking within the DRI-fed EAF route, offering a robust solution to the challenges posed by this pathway. With its array of benefits and innovative design, it paves the way for a greener, more efficient future in the steel industry.