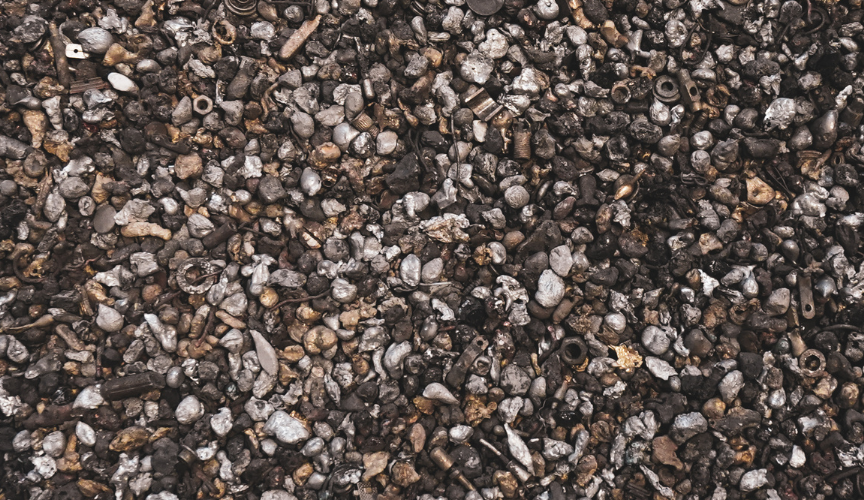
How much is the waste worth? The global value of the waste-to-energy market reached 35.1 billion U.S. dollars in 2019. By 2027, the waste-to-energy market is expected to be valued at 50.1 billion U.S. dollars, growing at a CAGR of 4.6% from 2020 to 2027.
However, not all countries worldwide yet know and enhance the potential of waste, which can become a valuable resource for generating energy and, at the same time, an environmentally sustainable choice.
Waste-to-Energy global status quo
What is the current situation regarding the Waste-to-Energy sector globally?
In total, Europe's waste-to-energy capacity amounted to 5.1 gigawatts. In Europe, there were already over 400 waste energy facilities, and another 300 in the rest of the world.
In 2022, Germany had the greatest installed capacity of municipal waste energy plants with 1,068 megawatts installed across the country.
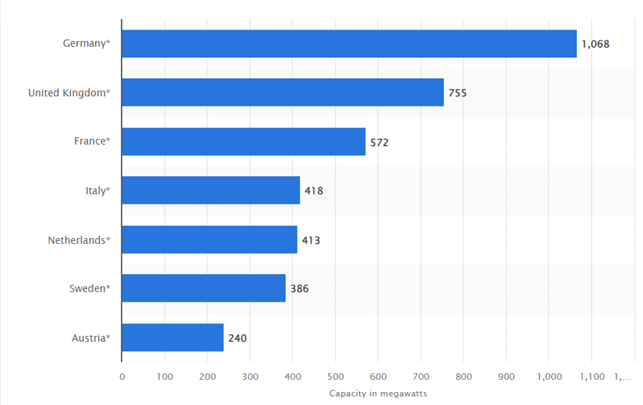
Installed capacity of municipal waste energy in Europe from 2010 to 2022, by Country (in megawatts) - Source: Statista
And what about the United States? Currently, in the US over half of the volume of municipal solid waste is discarded while the rest of household waste is either recovered or used to generate steam and electricity. Nowadays there are some 86 waste-to-energy facilities in the United States.
An even different situation concerns Southeast Asia where European firms are beginning to invest heavily in waste-to-energy (WtE) markets. According to energymonitor.ai, there are more than 100 waste-to-energy projects recently completed or underway in the Philippines, Indonesia, and Thailand.
European and Japanese companies have long dominated the WtE industry, while most other countries and regions in the world have very few incinerators or WtE plants. Most of municipal solid and commercial waste all over Asia is still landfilled or openly dumped. Recovering energy from incineration is, without a doubt, a more sustainable choice. That is why many cities are considering waste-to-energy.
Of course, it should be considered that in Asian landfills there is not as much separation of material between recyclables and non-recyclables. If not properly regulated, this could pose a problem for GHG emissions, and also because recycling, for most materials, is preferable and obviously more sustainable than incineration.
Waste to energy: How does it work?
In plain language, waste-to-energy (WtE) plants burn municipal solid waste (MSW) to produce steam in a boiler, and this steam is used to power an electric generator turbine or district heating. The incineration of municipal solid waste usually reaches temperatures of up to 1100°C. This kind of plants are increasingly being used in Europe as well as China and Japan.
In the past, this was an unregulated practice and therefore polluting. But now, due to stricter regulations and cutting-edge scrubbing technologies, modern WtE plants do not release as much pollution as in the past. And we can firmly say that waste is a much more sustainable choice than many other energy sources.
MSW is actually a mixture of energy-rich materials such as paper, plastics, yard waste, and products made from wood.
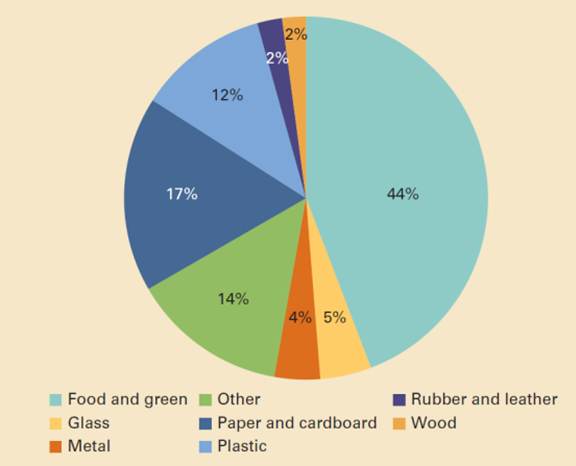
Source: the Global CCS Institute
But its value lies not only in its calorific power. There is much more: municipal solid waste incineration (MSWI) bottom ash contains economically significant levels of silver, gold, and other precious metals. The composition of IBA (incinerator bottom ash) depends on the composition of the burned waste; therefore, it may contain significant amounts of both ferrous and non-ferrous (NFe) metals.
Precious metals seem to come mainly from waste electrical and electronic equipment (WEEE) in parts smaller than 2mm, while some larger parts come from jewelry. The separation of precious metals from ashes may be profitable when considering the currently high prices of nonferrous metals.
Recovering precious metals from IBA
Recovery of NFe metals in IBA treatment is now a common practice due to modern technologies. But much depends on how the ash is extracted: wet or dry system.
Dry bottom ash extraction systems allow a higher rate of metal recovery.
Magaldi has been the first company worldwide to introduce the dry bottom ash handling technology, using ambient air instead of water during the extraction and cooling phases: the Magaldi Ecobelt® WA system.
The Ecobelt® WA improves the metal recovery rates by allowing the downstream recovery system to target smaller metal particles (< 0.3 mm). These recovery rates are significantly higher than the ones typically achieved from wet ash.
Also, the absence of water prevents further oxidation, providing cleaner metals that can go directly to the smelter. The enhanced metal recovery process also reduces the carbon footprint. It is estimated that the climate mitigation potential of metal recovery amounts to about 1 ton of CO2 equivalent for each ton of dry IBA treated, 5000 tons of treated IBA correspond to 20000 MWh district heating in terms of CO2 eq (source ZAR).
The remaining inert fraction could also be reused in the construction sector, mainly in road paving. On the contrary to wet ash, dry ash - extracted with Ecobelt® WA - contains low amounts of TOC. This makes it much more marketable to the construction industry, plus it is not a difficult residue to dispose of.
Waste-to-Profit
For more than one reason, WtE is a sustainable way to dispose of non-recyclable waste, deriving energy and environmental benefits in a sustainable manner.
Furthermore, dry IBA extraction and handling systems can provide advantages for WtE plants such as water and related cost savings, enhanced metal recovery, lower operating costs, higher boiler efficiency, process environmental sustainability, and marketable ash and metals.
A sustainable solution for the environment and institutions, a profitable one for firms investing in the WtE sector.