The Superbelt® HD conveyor
The critical reliability needed both to withstand severe shocks and convey heavy loads within the scrap preparation process
In steelmaking, there has been a significant increase in the use of recycled scrap, both in the EAF route and in integrated plants, as it reduces the need for additional resource extraction, saves energy consumption, and mitigates the environmental impact.
However, with steel scrap recycling, the ability to maintain the quality and performance of advanced steel grades has become a major concern. Before entering the steelmaking process, scrap needs preparation to remove contaminants, recover valuable materials (non-ferrous metals), and reduce the size of large parts into pieces small enough to enable transport and subsequent feeding into the steelmaking furnace.
Mechanical processes generally employed to prepare the steel scrap include baling, briquetting, shearing, and shredding. Moving a tough-to-handle material like steel scrap from one process to another requires heavy-duty conveyors capable of handling heavy, awkward loads, and enduring challenging environments.
The Superbelt® HD (heavy-duty) conveyors help automate the transport of materials before, during, and after the separation and preparation process, doing this job effectively and reliably. They reduce manual labor requirements, optimize recovery and increase overall efficiency in scrap processing by reducing maintenance, equipment jams, and downtime.
High reliability
The Superbelt® HD conveyor features partially overlapping steel pans securely bolted on a patented steel double-wire mesh system.
The belt damage-tolerant design is based on a multi-link concept: the mesh provides redundancy, little to no maintenance, and trouble-free continuous operation. Even in case the mesh gets severely damaged, the conveyor will keep running without sudden failures until the scheduled maintenance.
High impact toughness
The belt conveyor support structure features a shock-absorbing frame that absorbs the impact of falling material.
Specially designed carrying idlers are set along the belt width and can be closely spaced in the load zone. Mesh and belt pans can be made in manganese steel to ensure the highest resistance to both corrosion and deformation.
Safe operation & no material spillage
The Superbelt® HD conveyor provides great safety when transporting heavy steel scrap. High skirtboards follow the belt sidewall profile along its entire length to contain even the largest surges of material. Additionally, the high-pressure contact in the overlapping pan area creates a tight material seal which eliminates any spillage underneath the conveyor.
All of this contributes to creating a safer and more comfortable work environment.
Low maintenance requirements
As there are no chains, wheels, or sprockets, the only points requiring lubrication are head and tail pulley bearings and return idler bearings. Upper idlers and rollers are lubricated for life. Other elements are designed for continuous operation, and preventive maintenance can be carried out over a multi-year schedule.
Optional material weighing
The Superbelt® HD conveyor can also allow for optional material weighing. In this case, the weigh belt section is equipped with a special frame with load cells and an electronic control unit for real-time mass and rare calculations.
The actual material rate is determined by combining the belt speed, monitored by an encoder, and the weight signal given by the load cells.
Some successful stories
Italy
Heavy scrap conveying
Steel mill
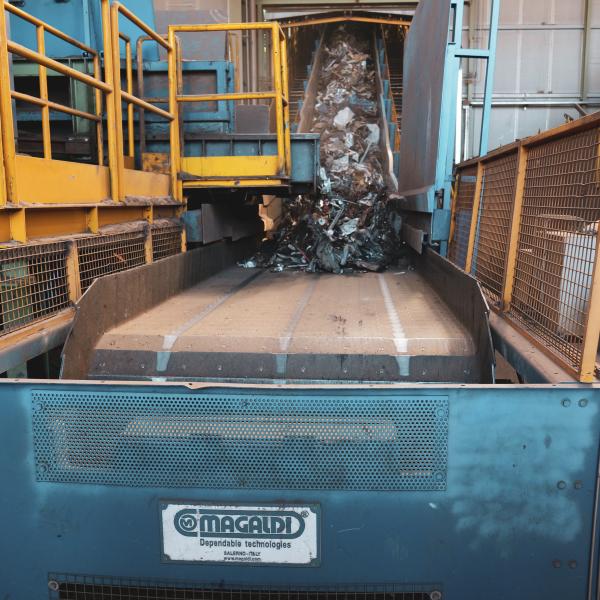
Designed tough to withstand the harsh conditions in the steel industry.
The Customer
A steel mill using “mini-mills ” EAF technology.
The Challenge
Provide a rugged conveyor to move heavy steel scrap within the scrap sorting and preparation area.
The Solution
Downstream the cleaning treatment, a Superbelt® HD conveyor transports 200 t/h of heavy scrap to the metal preparation area for furnace feeding.
The conveyor features unique supports and carrying idlers coated with rubber. The idler's closer pitch offers an optimal weight distribution on the belt, which, in turn, disperses the energy generated by falling scrap. Special sidewalls prevent material spillage while a weighing system installed on loading cells in the horizontal section allows for continuous weighing.
Finally, a rotating chute (60°) on a double slewing drive and a reinforced structure at the head section allow for the uniform spread of the material across various discharge points.