The Superbelt® conveyor
The best way to handle the “red rain” without generating much of fines and reducing power requirements
Mill scale is a very tempting industrial waste because of its richness in iron (about 72%), which makes it suitable for recycling either in sinter or pellet plants.
Although considered a “green waste” as it does not generally contain any inflammable, toxic, or corrosive material, its recovery from underneath the rolling line poses demanding challenges due to high temperatures, fugitive dust, and material spillage.
The Magaldi Superbelt® conveyor has proven to be key to the conversion of mill scales from waste to valuable products.
High reliability
The Superbelt® conveyor features partially overlapping steel pans securely bolted on a patented steel double-wire mesh system.
The belt damage-tolerant design is based on a multi-link concept: the mesh provides redundancy, little to no maintenance, and trouble-free continuous operation. Even in case the mesh gets severely damaged, the conveyor will keep running without sudden failures until the scheduled maintenance.
High temperature resistance
With the Superbelt® conveyor, high temperatures issues are solved thanks to the patented method of connecting the pans to the mesh belt, which leaves all components free to thermally expand in any direction without permanent deformation. As a result, the conveyor is able to withstand temperatures of up to 1,100°C.
Reduced dust emissions
Due to the fine particle size, the mill scale can easily escape and dirty the deep and long pit underneath the rolling line, not easy to reach and clean.
The classical solution used to handle the hot mill scale involves the use of a series of vibrating conveyors. However, they proved to be unreliable, very noisy, high-maintenance, and liable for fine particle release during conveying.
Low power consumption
Designed to avoid sliding friction among the moving parts, the Superbelt® conveyor not only prevents equipment wear but also ensures low power consumption.
The smooth and vibration-free running also contributes to lower energy consumption, which is about one-tenth of vibratory conveyors' requirements.
The amount of energy savings also depends on the conveyor length. As such, with the Superbelt®, the longer is the conveyor installed underneath the rolling line, the greater the energy savings will be.
Better environmental compliance
The proper management of mill scale is not only a matter of profitability but also an environmental issue due to ever-tightening regulations.
When dumped in landfills, the mill scale can result in the leaching of some percentages of heavy metals into soil and groundwater, thus threatening the environment. The continuous demand for more landfills and their bad effect on the environment highlights the need for more productive utilization of mill scale.
Some successful stories
Canada
Hot scales conveying
Hot rolling mill
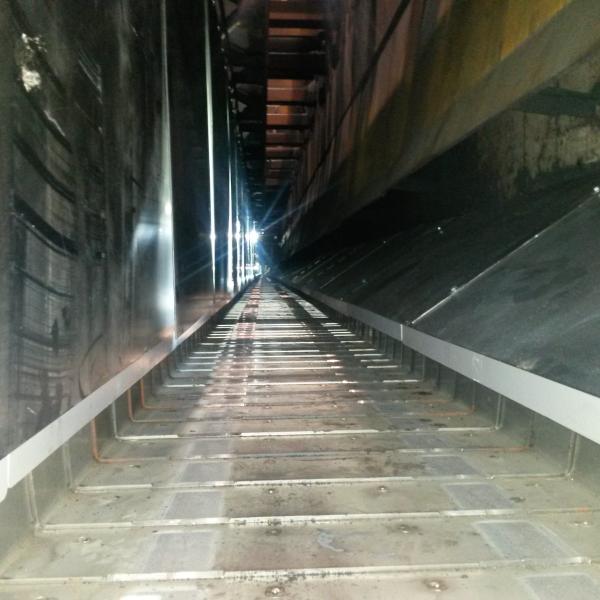
The Superbelt® conveyor greatly reduced energy consumption requirements.
The Customer
Canada’s leading steel producer, working with top automotive, energy, packaging, and construction brands. The integrated steel complex produces 4.5 million net tons of high-quality flat carbon annually.
The Challenge
As part of a wider project to reduce energy consumption in the hot rolling mill, Magaldi was requested to investigate the possibility to replace 27 shaking tables for hot scales conveying, responsible for high energy consumption and material spillage in the pit underneath the rolling strend.
The Solution
A 90m long Superbelt® conveyor collects the mill scales falling from the rolling strand at 800°C, and moves them up to the discharging beam. Its rated power is just 4 kW while power consumption is even lower. A significant energy saving was achieved when compared to the existing 27 shaking tables. Additionally, thanks to its smooth transport without vibrations, the Superbelt® conveyor allowed to dramatically decrease to 5% the pit cleaning requirement.