The Superbelt® conveyor
Ideal for transporting the poured molds from the in-mold cooling conveyor or the punch-out station to the shakeout
High reliability
The Superbelt® conveyor is made up of partially overlapping steel pans securely bolted on a patented steel double-wire mesh system, supported by carrying idlers along its entire width. At the loading points, the carrying idlers can be closely spaced or mounted onto a shock absorber frame to accommodate even large molds.
The belt design is based on a multi-link concept that ensures redundancy, little to no maintenance, and trouble-free continuous operation. Even if the mesh is severely damaged, the conveyor will keep on running till the scheduled maintenance, without sudden failures.
The trouble-free operation allows to preserve the productivity and profitability of the whole plant and results in greater efficiency and uptime during 24/7, year-round operation.
Reduced silica dust emissions
As the molds are generally cracked open at the loading point, the conveyor can be equipped with a dust cover with dust collection pick-up points.
However, thanks to the gentle and smooth transport with no vibrations, the Superbelt® conveyor enables minimal silica dust generation and emissions. This reduces workers' exposure to airborne silica dust and, along with noise at minimum levels, contributes to a healthier and more comfortable working environment.
Green sand applications
In the case of green sand applications, the Superbelt® conveyor does not need to be equipped with heaters as for traditional vibratory technologies. The molds are transported with no relative motion against steel parts, thus the risks of sand sticking and accumulation are completely overcome.
Some successful stories
Italy
Mold dump conveying
Iron foundry
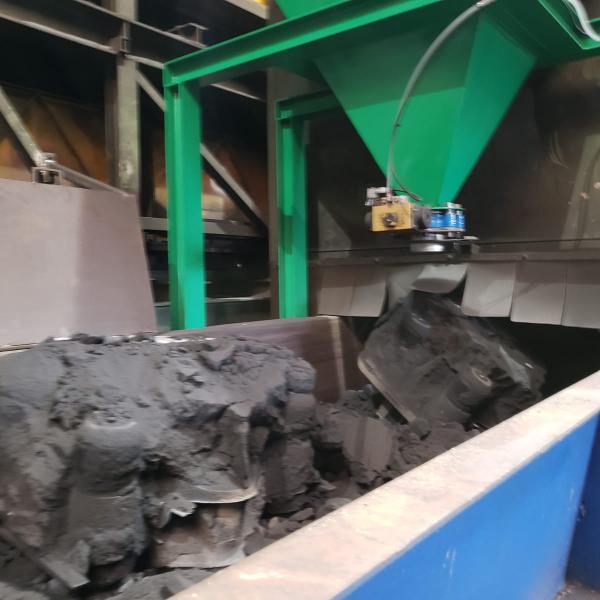
The Superbelt® conveyor allowed to contain dust, eliminate spillage, and reduce cleanup and maintenance efforts.
The Challenge
The foundry was experiencing severe sand spillage at an apron conveyor used to transport molds. Material spillage significantly eroded productivity and throughput, requiring frequent equipment stoppages and high cleaning costs.
The Solution
The horizontal section of the mold dump Superbelt® conveyor is armoured to absorb the shock of 220 molds/h. The second inclined (25°) section allows discharging the molds into the digger drum. The conveyor is equipped with a Spill-chain installed underneath the sloping section, and a motorized brush at the head drum to collect any sand that may detach from the pans.
The Superbelt® conveyor only needs standard maintenance because 99% of the material stays in the production flow.