The Superbelt® conveyor
Suitable to safely handle large volumes of aluminum scrap
The efficient collection and treatment of scrap is a matter of growing importance to the profitability of aluminum foundries. Scrap value, labor savings, energy consumption, and workers’ safety are all factors that are affected, for better or worse, by the scrap handling system.
Thanks to its unique design, the Superbelt® conveyor gives aluminum foundries the advantage and flexibility over fork trucks, rubber belts, and apron conveyors, in transporting manufacturing scraps (sprues, gating, risers, casting trim, rejects). It is generally used for feeding balers, shredders, and remelt furnaces, or for transporting the scrap from the die-casting process to the scrapyard.
High reliability
The Superbelt® conveyor features partially overlapping steel pans securely bolted on a patented steel double-wire mesh system.
The belt damage-tolerant design is based on a multi-link concept: the mesh provides redundancy, little to no maintenance, and trouble-free continuous operation. Even in the case the mesh gets severely damaged, the conveyor will keep running without sudden failures till the scheduled maintenance.
The trouble-free operation ensures productivity and profitability and results in greater efficiency and uptime during a 24/7, year-round process.
Jam-free operation design
Due to sharp edges, thin projections, and irregular shapes, aluminum scrap tends to become caught in the belt.
With the Superbelt® conveyor, this issue is solved thanks to the tight pan structure featuring a perfect fit in the overlap area for an effective seal. This feature prevents material from snagging or getting stuck, thus avoiding conveyor jam-ups or damage.
Safe operation
Eliminating manual scrap handling keeps operators safe and more productive.
By completely automating the scrap return process, the Superbelt® conveyor minimizes safety risks related to forklift traffic and operators’ exposure to falling scrap. The conveyor design, featuring high skirtboards that follow the belt sidewall profile along its entire length, prevents material overflow during transportation.
Low power consumption
Designed to avoid sliding friction among the moving parts, the Superbelt® conveyor is very energy-efficient. Its power demand is about one-tenth of that of vibratory conveyors.
Optional material weighing
The Superbelt® conveyor can optionally allow for material weighing. In this case, the weigh belt section is equipped with a unique frame with load cells and an electronic control unit for real-time mass and rate calculations.
The actual material rate is determined by combining the belt speed, monitored by an encoder, and the weight signal given by the load cells.
Some successful stories
Italy
Aluminum scrap conveying
Aluminum foundry
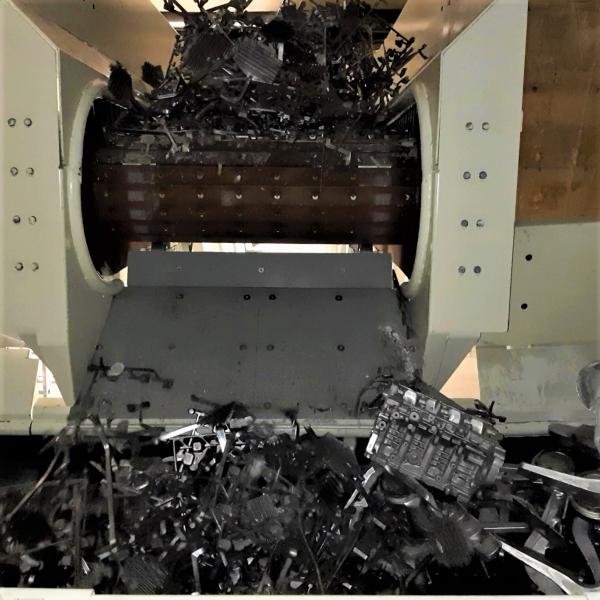
The Superbelt® conveyors offered greater efficiency, reduced material handling cycle time, and increased safety for operators.
The Customer
The foundry is specialized in aluminum castings for the automotive industry in Loast Foam, Low Pressure and High Pressure Die Casting technologies.
The Challenge
Prior to the Superbelt® conveyor installation, the rejected castings coming from the HPDC machines located on the upper floor were manually discharged into bins placed in a basement. As these operations placed severe safety concerns, the Customer decided to automate the scrap handling process.
The Solution
Installed in a basement, a long Superbelt® conveyor collects sprues, gates and rejected castings coming from 7 HPDC machines located on the upper floor. This conveyor transfers the material to a shorter Superbelt® that ramps outside the basement to discharge the material into scrap bins for subsequent remelting.