The Magaldi Quenching Conveyor (MCC® AL)
Deployed for faster and uniform cooling of aluminum parts, it offers huge advantages over a typical T6 heat treatment process
Quenching is the most critical operation in the entire process of heat-treating aluminum.
The mechanical properties of aluminum cast parts are critically dependent on the rate at which the part is quenched after the forming operation. On the one hand, the fastest quenching rate allows for high resistance to corrosion and the best combination of strength and toughness; on the other hand, residual stresses and distortion increase with increasing quench rates. Hence, a balance between the maximum quench rate and distortion must be maintained.
Through a properly engineered system, Magaldi provides the quenching rate best suited to meet the desired properties. The combined use of analytical methods (i.e. CFD analysis), experimental tests, and in-field measurements, allows for the design of custom-tailored solutions where specific cooling rates are achieved to ensure the proper metallurgical microstructure in the final material.
Working concept
The MCC® AL conveyor is designed for both cooling down the castings and as final heat treatment (T5 - air quench) in a more timely and efficient manner.
It is comprised of:
- the Superbelt® conveyor as the key component.
The belt design is based on a multi-link concept which ensures redundancy, little to no maintenance, and trouble-free continuous operation, thus avoiding costly disruptions. - A cooling tunnel held under negative pressure.
A stream of ambient air at a controlled speed flows over the castings to rapidly cool them from above their critical temperature. - An optical detector that ensures the proper functioning of the belt at almost zero speed or batch.
Engineered cooling process
For each and every project, Magaldi thoroughly investigates the thermal properties both of air and castings, to deliver the most efficient cooling process.
The combined use of analytical methods (i.e. CFD analysis), experimental tests on the in-house built test rig, and in-field measurements have allowed for very accurate thermodynamic models to be created and tested for ensuring effective modeling and, ultimately, the cooling process.
Effective air-blast quenching
With the MCC® AL, castings are drastically cooled down from the molding temperature (about 450 °C) to room temperature, typically in the range of 150-200 °C.
By guaranteeing a cooling rate of up to 50 °C/min, it is possible to avoid aluminum reheating. Thus, the MCC® AL offers huge advantages as far as time, energy consumption, and capital investment over a typical T6 heat treatment process (treatment + quenching + artificial aging).
Integrated Supervision System (optional)
The MCC® AL conveyor can be integrated with the MISS®, a highly dynamic control system that reliably checks the cooling parameters and automatically adjusts the belt speed and the cooling rate to enhance the process.
Additionally, with the MISS® all process-relevant data are available. Once set, the parameters are continuously recorded and can be restored at any time. This means that the cooling process is reproducible and this, in turn, increases the quality of the cast parts and reduces scrap rates.
Some successful stories
Mexico
Air quenching
Aluminum foundry
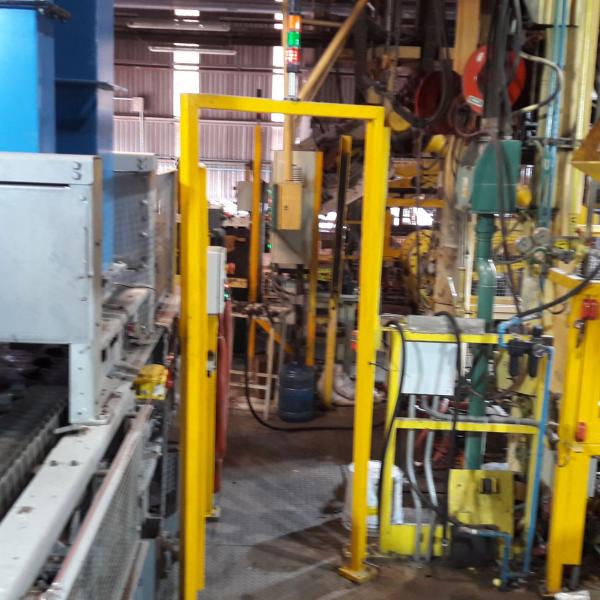
The MCC® AL has proven to be successful in reducing cooling times and ensuring greater cooling effectiveness and uniformity.
The Customer
Leading provider of light-weighting solutions for the global automotive industry. The foundry in Mexico is one of the 38 facilities owned in 16 countries.
The Challenge
A few years before, Magaldi had already partnered with the Customer, supplying its casting cooling technology to one of the Group’s foundry. After experiencing the benefits provided by the MCC® AL conveyor, the Customer decided to rely on Magaldi for a new and even more ambitious project: to design a casting cooler able to quench by air the aluminum castings.
The Solution
Custom-engineered to meet application requirements, the MCC® AL can be used for T5 heat treatment. Installed downstream of the molding lines, 6 MCC® conveyors work in batch to cool castings down from 460±20°C to 100±50°C in about 7 min. This means a cooling rate of 50°C/min, which makes it no longer necessary re-heat the castings, thus reducing operating time and costs.