The Superbelt® conveyor
Ideal for high temperature applications and demanding service conditions
High temperatures, dust, and material abrasiveness are the most damaging issues to conveyor systems in cement plants, responsible for premature equipment wear and high maintenance costs.
Thanks to the smooth running and the excellent resistance to abrasion and high temperatures, the Superbelt® conveyor is widely used for hot clinker transportation, providing high performance, safe and dust-free operation, and longer service life.
Its full potential comes to force in the case of retrofit projects when used to replace rubber belts, Apron-based or pan conveyors. It can be integrated into newly-built or existing production lines according to process requirements and layout constraints.
High reliability
The Superbelt® conveyor features partially overlapping steel pans securely bolted on a patented steel double-wire mesh system.
The belt damage-tolerant design is based on a multi-link concept: the mesh provides redundancy, little to no maintenance, and trouble-free continuous operation. Even in case the mesh gets severely damaged, the conveyor will keep running without sudden failures until the scheduled maintenance.
The trouble-free operation ensures productivity and profitability and results in greater efficiency and uptime during a 24/7, year-round process.
High conveying capacities
The Superbelt® conveyor ensures the design conveying capacities by a combination of the belt speed and the height of the sidewalls.
In the case of greenfield projects, a compact arrangement of the belt pans width and sidewall heights is selected to meet the project requirements.
High temperature resistance
With the Superbelt® conveyor, high temperatures issues are solved thanks to the patented method of connecting the pans to the mesh belt, which leaves all components free to thermally expand in any direction without permanent deformation. As a result, the conveyor is able to withstand temperatures of up to 1,100°C.
Reduced dust emissions
The smooth running without vibrations minimizes dust emissions, while the tight structure of the steel pans prevents any spillage thanks to the perfect fit in the overlap area. Whenever dust containment is a priority, Magaldi can provide a fully-sealed conveyor (Ecobelt®) featuring a steel casing for more effective dust control.
Low noise emissions
The lack of chains and sprockets (and the related mechanical engagement), and the absence of relative motion among rollers and steel parts, allow the Superbelt® to run at a low noise level, generally below 75 dB(A).
Low maintenance requirements
In the case of conventional Apron-based or pan conveyors, frequent maintenance interventions are paramount to avoid the conveyor collapsing due to unpredictable chain breakages. Lubrication must be, therefore, frequently performed although grease represents a detriment to the environment and the conveyor itself since clinker dust can get stuck and settle in the chain links, leading to wear issues.
On the contrary, the maintenance demand of the Superbelt® conveyor is very limited thanks to its design devoid of chains, sprockets, hinges, and pins. The only points requiring lubrication are the head and tail pulley bearings, which can be greased with the belt running. The other components are designed for continuous operation and can be checked during preventive maintenance over a multi-year schedule.
Extra long service life
Thanks to the unique design that combines both heat and wear resistance, the Superbelt® conveyor ensures a service life longer than any other competing technology.
Just think that a Superbelt® conveyor installed in a cement plant in Sardinia (Italy) has been operating since 1981 with the original belt. In its 40+ years of operation, this conveyor has handled more than 33 million tons of clinker with a small maintenance demand.
Reduced CapEx
The Superbelt® conveyor can be easily retrofitted into the existing frames of conventional conveyors, without major modifications. This reduces the CapEx (no additional costs for dismantling the old equipment frame nor for building the new one) and slashes the rotary kiln outage time to the bone.
Some successful stories
USA
Hot clinker conveying
Cement plant
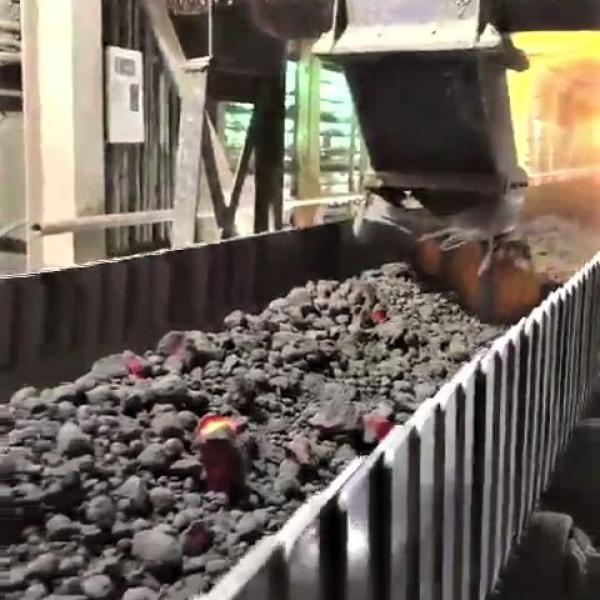
The Superbelt® conveyor proved to be both durable and capable of withstanding hot and abrasive materials.
The Customer
Cement plant in San Antonio, TX.
The Challenge
The rubber belt conveyor used to transport hot clinker had a very limited capability to withstand high temperatures. Additionally, the abrasive nature of the transported material caused rapid belt wear phenomena, resulting in premature equipment failure and long downtime.
The Solution
A Superbelt® conveyor transports about 170 t/h of hot and abrasive clinker round the clock. The unique combination of both heat and wear-resistant features allowed to overcome all concerns experienced with the previous equipment. Reliability, higher uptime, and reduced O&M costs are just some of the benefits provided. By integrating the Superbelt® conveyor into the existing frame of the rubber belt (with minor changes), Magaldi also succeeded in reducing the CapEx.
Senegal
Hot clinker conveying
Cement plant

Tight space and steep inclinations are regarded as preferred application conditions for the Superbelt® conveyor.
The Customer
The most modern cement plant in Africa.
The Challenge
The existing apron conveyor was responsible for material spillage and was extremely high in maintenance due to frequent chain link breaking caused by uneven heating and cooling cycle. But the most challenging aspect was the extreme inclination the conveyor had to reach.
The Solution
Fitted with transversal cleats to prevent the material from rolling back, the Superbelt® conveyor transports 150 t/h of cement clinker at 680°C across an inclination of 54°.
In addition to ensuring high availability and dependability, Magaldi also reduced the project CapEx by using the same supporting structures – with minor changes - of the existing apron conveyor.