The Ecobelt® WA system
Unique system for dry extraction, air cooling, and mechanical conveying of Incinerator Bottom Ash (IBA)
Given the pressure to achieve the decarbonization goals and adopt circular economy models, the valorization of IBA has become essential to achieve a paradigm shift from cost to profit and sustainability.
Applying the dry approach in IBA extraction gains several economic advantages while reducing the ecological footprint of WtE plants.
IBA weight reduction
By eliminating the water, the weight of the IBA is reduced by approximately 20 wt.-%.
The weight reduction can result in large transportation and landfill fee savings.
Water and water-treatment elimination
Discharging IBA in a dry manner results in the effective mitigation of the environmental impact and a high reduction in operating costs that comes along by eliminating the need to dispose of or treat the polluted water.
TOC Reduction
The dry discharge approach enables after-burning within the discharge area, which can reduce the residual Total Organic Content (TOC) in the IBA below 0.5%.
Moreover, the remaining heat in the IBA, which would otherwise be lost in the water bath, can be fully recovered.
Increased metal recovery and
IBA aggregates utilization
Since no water is added to the IBA, a higher metal recovery can be achieved, especially in the finer fractions.
By recovering more heavy metals, the quality of the IBA aggregates is more favorable for further utilization.
The Superbelt® conveyor technology
The Ecobelt® WA system utilizes the patented Superbelt® conveyor, enabling reliable transportation of extremely hot, sharp, and abrasive bottom ash, even under challenging conditions.
This technology provides several competitive advantages, including higher dependability, resistance to high temperatures, high impact toughness, minimal wear and tear, low power demand, easy maintenance, and an extended service life.
Some successful stories
Switzerland
Wet-to-Dry conversion
Waste-to-Energy plant
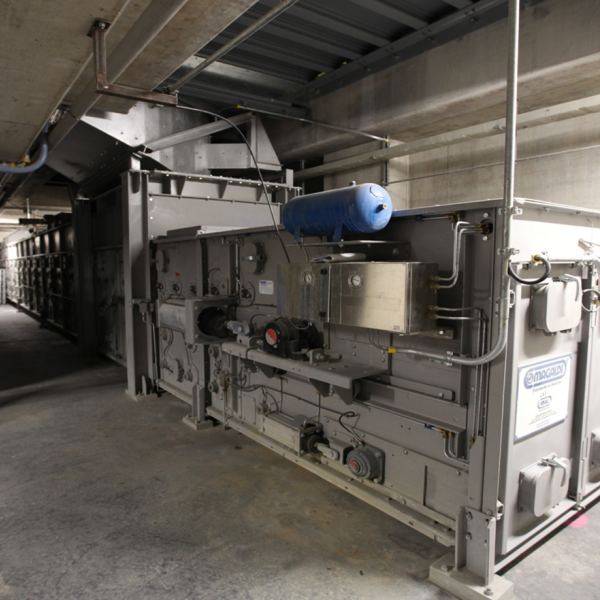
The dry IBA extraction has been the key feature to gaining a more effective separation and recovery of metals and minerals from the ash mixture.
The Customer
The WtE plant consists of 3 combustion lines burning household and industrial waste. It is the first fully-dry IBA treatment plant in the world.
The Challenge
The Customer was in need to replace an apron-based conveyor collecting the dry bottom ash from the combustion lines #2 & 3.
Some time later, Magaldi also carried out the wet-to-dry conversion of the bottom ash handling system on the incineration line #1.
The Solution
An Ecobelt® WA conveyor transports the dry bottom ash from lines #2 & 3 up to the dry ash treatment and the metal recovery facility.
Installed in place of a wet hydraulic ram and the downstream rubber belt conveyor, a second Ecobelt® WA transports:
- the hot bottom ash and the siftings ash produced by the line #1
- the hot bottom ash produced by lines #2 & 3.
The Ecobelt® WA system allowed overcoming all issues of poor reliability, unpredictable outage, and pulse waves back to the furnace, generated by the existing systems.
Italy
Dry Incinerator Bottom Ash handling
Waste-to-Energy plant
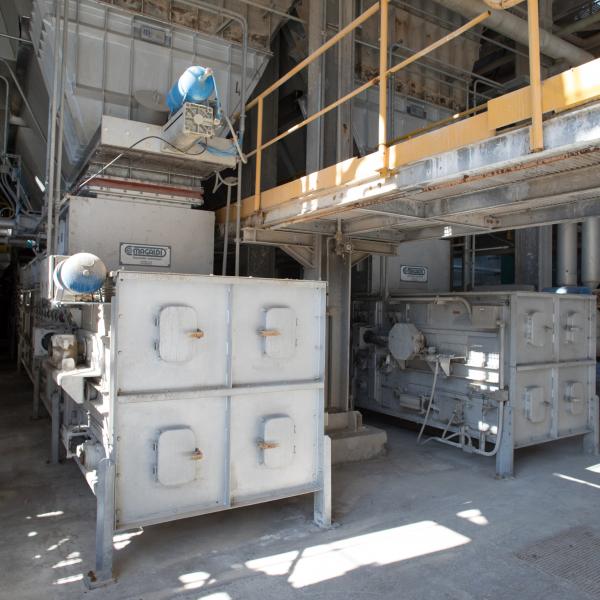
The Ecobelt® WA overcame maintenance headaches and all issues of poor reliability, unpredictable outage, and safety hazards.
The Customer
The WtE plant consists of 3 combustion lines, designed to thermally convert about 397,000 tons per year of secondary solid fuel (SSF).
The Challenge
Magaldi was selected to carry out the wet-to-dry conversion of the IBA handling system on the twin combustion lines #2 & 3. The existing submerged apron-based conveyors were placing serious problems:
- IBA with a high moisture content (>25%), thus increasing the disposal costs;
- frequent clogs affected the normal operation, posing safety hazards too;
- no maintenance could be carried out with the wet IBA system in operation.
The Solution
Each combustion line is equipped with 2 Ecobelt® WA conveyors which transport and cool down both the IBA and the sifting ash in a completely dry way.
Downstream the Ecobelt® WA conveyors, ash is conditioned by using a small amount of water to keep the dust down and allow safe transportation to the metal recovery facility.
Japan
Wet-to-Dry conversion
Waste-to-Energy plant
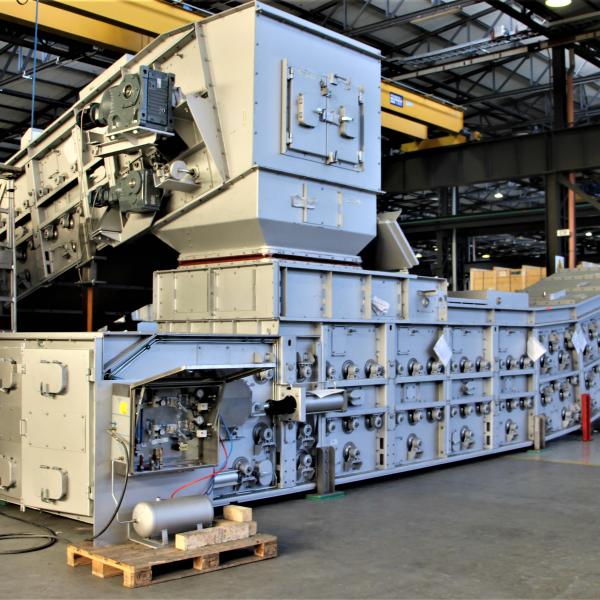
The Ecobelt® WA system has proven to be rated the best in the market in terms of operational costs and environmental protection.
The Customer
The plant consists of 2 combustion lines, each burning municipal solid waste up to 350 tons/day. The overall power output is 15 MWe.
The Challenge
The Customer aimed at replacing the existing wet submerged chain conveyors with a more dependable, environmentally friendly and easy-to-maintain technology.
The Solution
The Ecobelt® WA conveyors provided both technical and economic benefits for the IBA cooling and handling. The dry IBA handling systems do not require water both for cooling and conveying, thus leading to water savings and complete elimination of costs associated with wastewater treatment. Moreover, ferrous metals are recovered more efficiently from the dry IBA.