The Superbelt® HD conveyor
A safer and more reliable alternative to magnets and buckets for improving the EAF scrap route
Due to the growing environmental concerns for greenhouse gas emissions and the economic advantages of metal recycling, there has been a significant increase in the use of metal scrap, both in EAF/smelter and in integrated plants. In both cases, the scrap handling process poses extreme requirements due to the need to handle huge quantities of material, sometimes in large, heavy and/or sharp chunks.
Magaldi designed a heavy-duty scrap conveyor able to connect the scrap yard to the EAF/smelter, ensuring safe material handling and offering high flexibility in furnace feeding.
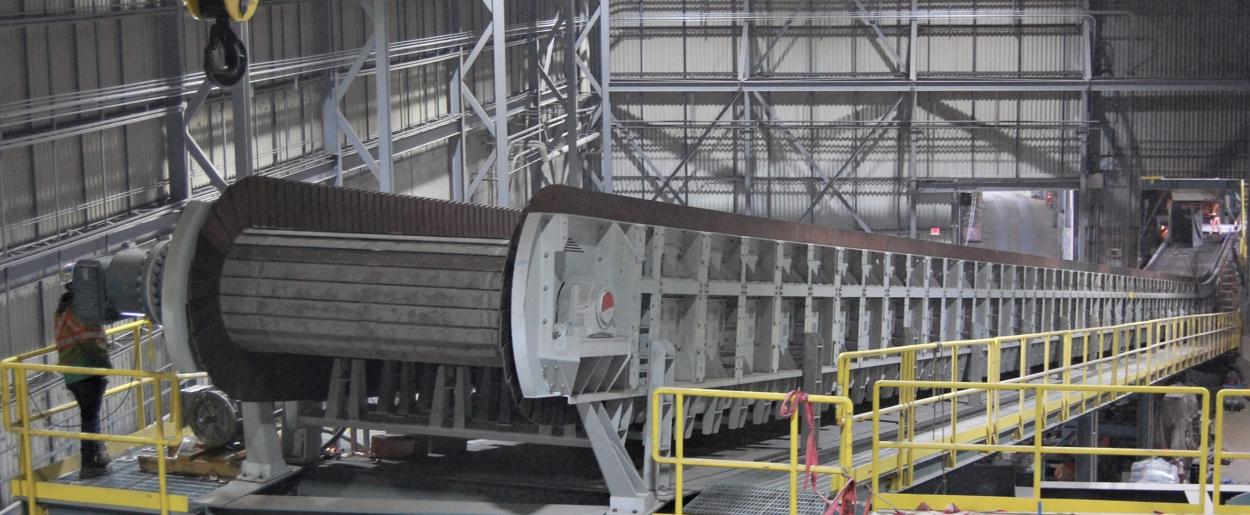
High reliability
The Superbelt® HD conveyor features partially overlapping steel pans securely bolted on a patented steel double-wire mesh system.
The belt damage-tolerant design is based on a multi-link concept: the mesh provides redundancy, little to no maintenance, and trouble-free continuous operation. Even in case the mesh gets severely damaged, the conveyor will keep running without sudden failures until the scheduled maintenance.
High impact toughness
The belt conveyor support structure features a shock-absorbing frame that absorbs the impact of falling material.
Specially designed carrying idlers are set along the belt width and can be closely spaced in the load zone. Mesh and belt pans can be made in manganese steel to ensure the highest resistance to both corrosion and deformation.
Safe operation
The Superbelt® HD conveyor provides a high safety degree when transporting heavy steel scrap.
High skirtboards follow the belt sidewall profile along its entire length to contain even the largest surges of material. Additionally, the high-pressure contact in the overlapping pan area creates a tight material seal which eliminates any spillage underneath the conveyor.
All of this contributes to creating a safer and more comfortable work environment compared to the typical standards of the steel industry.
High flexibility
The Superbelt® HD conveyor offers high flexibility in furnace feeding.
When using magnets/buckets, the EAF/smelter can work exclusively in batches. In contrast, wherever the EAF/smelter features an accumulation hopper, the Superbelt® HD conveyor allows continuous furnace feeding. It means shortening power-on-time, increasing productivity, and lowering power demand.
Moreover, since the electric arc works on a liquid bath, the steel in the furnace is in a better metallurgical equilibrium.
Optional material weighing
The Superbelt® HD conveyor can also allow for optional material weighing. In this case, the weigh belt section is equipped with a special frame with load cells and an electronic control unit for real-time mass and rate calculations.
The actual material rate is determined by combining the belt speed, monitored by an encoder, and the weight signal given by the load cells.
Some successful stories
Canada
Heavy scrap conveying
Hot rolling mill
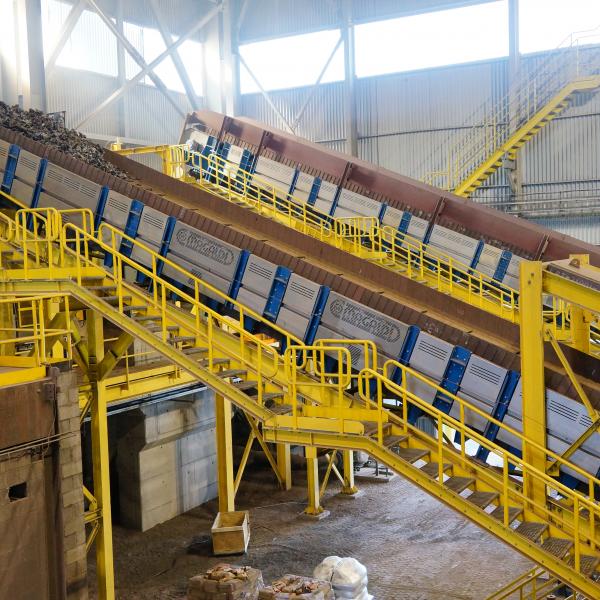
The Superbelt® HD conveyors proved to be particularly well suited for continuous or batch feeding of heavy steel scrap.
The Customer
Steelmaking facility producing steel billets and hot rolled wire roads from metal scrap.
The Challenge
The EPC contractor requested Magaldi to provide a dependable solution to handle the increased scrap charging volume (200 t/h) and reduce operating costs associated with the furnace bay crane used for buckets charging in the Rolling Mill.
The Solution
Two parallel Superbelt® HD conveyors feed the downstream slip-stick pan conveyor which preheats the scrap and discharges it into the EAF. Both conveyors are batch loaded by a magnet or a grapple that discharges up to 5 tons per shot of heavy scrap with large beams and scrap clusters up to 1500 mm and 300 kg each. The Superbelt® loading section has been designed very sturdily to withstand such tough conditions. At the discharge point, a frequency converter adjusts the belt speed to properly feed the slip-stick conveyor. A weighing device installed upstream of the conveyors provides basic information to coordinate the EAF energy usage and the scrap feed rate.
USA
Heavy scrap conveying
Integrated steel plant
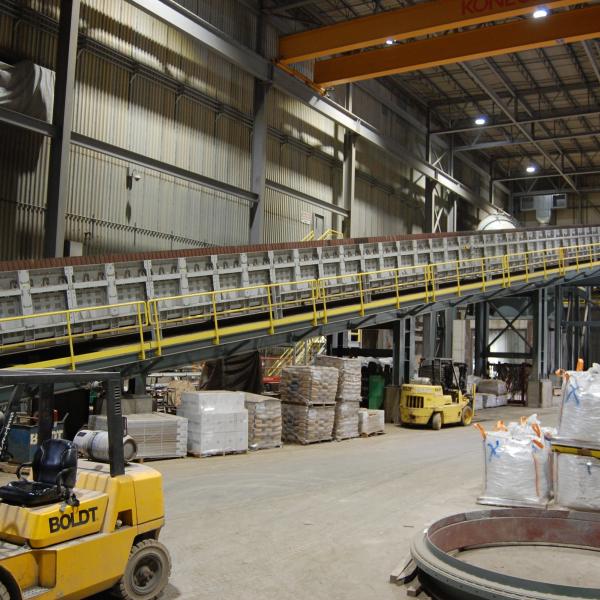
Suited for the most challenging applications, the Superbelt® HD conveyor offers unmatched ruggedness and reliability.
The Customer
Integrated steelmaker, whose capabilities include steel melting, bar and rod rolling, coil processing, and wire drawing. The plant is home a fully integrated mini mill that includes a melt shop, a rolling mill, and a processing facility.
The Challenge
Magaldi was involved in the most challenging project ever carried out in the steel industry: to install a huge conveyor to collect and convey up to 300 t/h of heavy steel scrap.
The Solution
Charged by a Tenova Consteel, the Superbelt® HD conveyor is 2.400 mm wide, with belt pans in manganese steel (Hardox 400) and 400 mm sidewalls placed along the entire length of the belt to prevent scrap from falling out. The loading area is designed with special supports and carrying idlers coated with rubber rings, installed with a closer pitch, to withstand heavy impact loads.