The Superbelt® conveyor
Suitable to meet the severe conditions found underneath shears
Tube and pipe producers need to maximize uptime and boost scrap recycling now more than ever. In line with circular economy principles, all scrap from downstream pipe/tube production is collected and reused in the steelmaking process to cut down production costs and minimize the environmental footprint of the business. However, this process places severe requirements on material handling equipment as tube and pipe scrap come out of the shears in many different shapes and weights.
Made with very strong and heavy construction, the Superbelt® conveyor has the potential to handle a variety of shear scrap, providing all the flexibility needed in scrap processing operations.
High reliability
The Superbelt® conveyor features partially overlapping steel pans securely bolted on a patented steel double-wire mesh system.
The belt damage-tolerant design is based on a multi-link concept: the mesh provides redundancy, little to no maintenance, and trouble-free continuous operation. Even in case the mesh gets severely damaged, the conveyor will keep running without sudden failures until the scheduled maintenance.
High impact toughness
The belt conveyor support structure features a shock-absorbing frame that absorbs the impact of falling material.
Specially designed carrying idlers are set along the belt width and can be closely spaced in the load zone. Mesh and belt pans can be made in manganese steel to ensure the highest resistance to both corrosion and deformation.
Safe operation & no material spillage
The Superbelt® conveyor provides a high safety degree when transporting shear scrap.
High skirtboards follow the belt sidewall profile along its entire length to contain even the largest surges of material. Additionally, the high-pressure contact in the overlapping pan area creates a tight seal which eliminates any spillage and avoids any risk of material impingement due to the sharp edges.
All of this contributes to creating a safer work environment.
Optional material weighing
The Superbelt® conveyor can also allow for optional material weighing. In this case, the weigh belt section is equipped with a special frame with load cells and an electronic control unit for real-time mass and rate calculations.
The actual material rate is determined by combining the belt speed, monitored by an encoder, and the weight signal given by the load cells.
Some successful stories
Mexico
Shear scrap conveying
Integrated seamless pipe mill
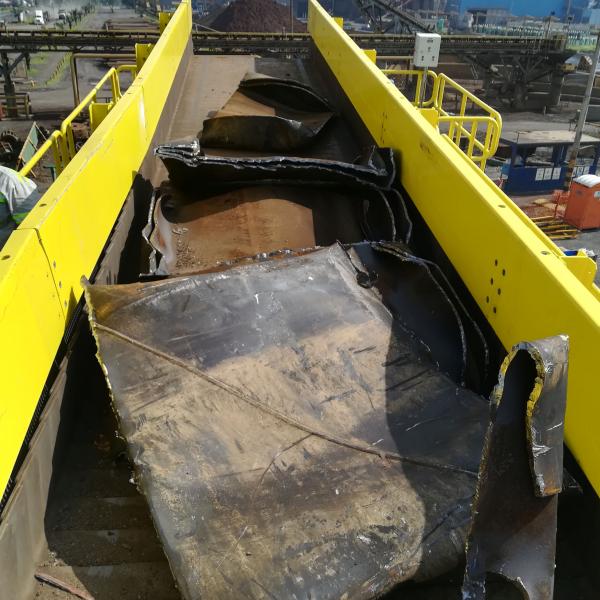
Due to their highest level of flexibility, the Superbelt® conveyors enabled the optimal distribution of steel scrap over the entire available floor space.
The Customer
Steel is produced from scrap metal and sponge iron turned into billets and transformed into seamless pipes. Steel scrap resulting from pipes cut is used to feed an EAF.
The Challenge
Originally scrap was transported by trucks to the melt-shop. This process was very expensive and caused inefficiencies in the management of available space.
The Solution
Magaldi installed 2 Superbelt® conveyors to move pressed tubular scrap (90%) and other metallic scrap (10%) from the automatic shear machine up to the scrap yard. The first conveyor is fixed and made of steel wear pans with formed swells and reinforcing ribs. The loading area is designed to withstand the impact of heavy pieces discharged from the shredding pivoting conveyor. Additionally, both sides of the conveyor channel are lined with wear-resistant pans to minimize friction and material jamming.
The second Superbelt® conveyor is designed to pivot over a curved steel rail. Thanks to its exclusive design, the conveyor gives the opportunity to discharge the material over a larger area of the scrapyard, thus making the most of the available space.
USA
Shear scrap conveying
Integrated mini mill
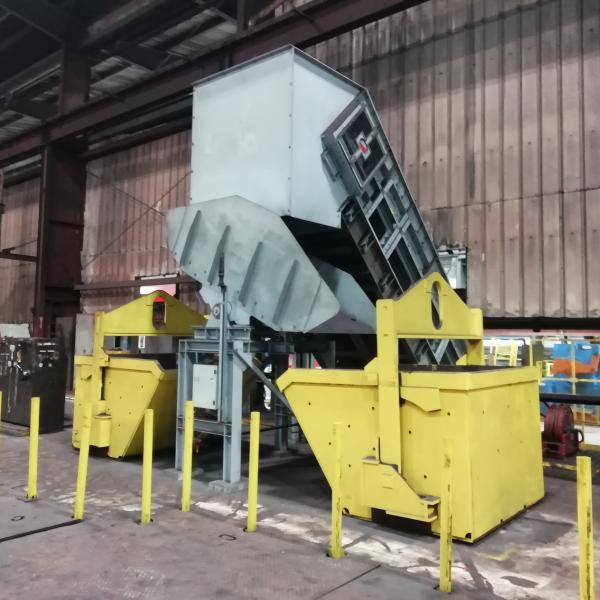
Suited for more extreme temperatures and demanding heavy-duty operating conditions.
The Customer
Fully integrated mini mill with a state-of-the-art melt shop and a rolling mill.
The Challenge
The Customer had to equip the melt shop with a reliable conveyor able to handle high-temperature shear scrap.
The Solution
A Superbelt® conveyor moves cropped bars from the shear machine to the operating floor, where the material is discharged in two buckets. A discharge chute diverts the bars into the buckets to discharge the first one while the second one is being filled.
Designed with a 45° slope, the Superbelt® conveys two types of hot (1,093°C) shear scraps:
- crop cuts, in regular operating conditions;
- cobble cuts, in upset conditions.
Based on the design data, the crop cuts rate is 3.05 MTPH while, in upset conditions, the surge capacity required to convey cobble cuts is 272.2 MTPH. In the latter case, the overall mill control system automatically adjusts the belt speed till the upset condition is overcome. For this reason, a frequency converter has been installed on the conveyor’s drive.
USA
Shear scrap conveying
Pipe mill
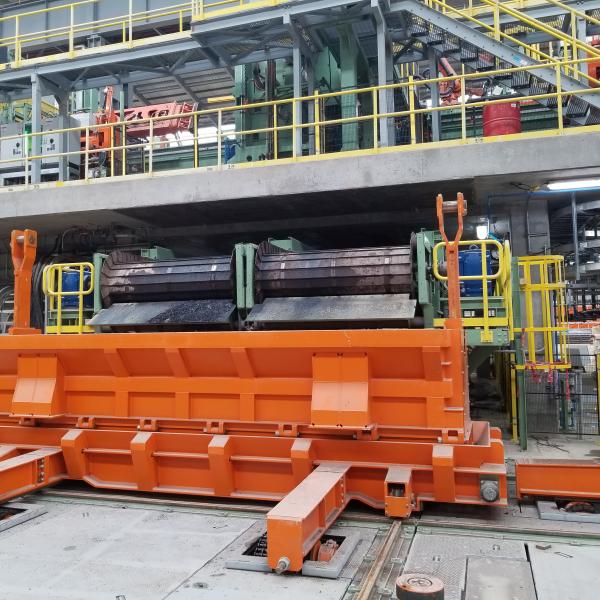
Suitable to meet the severe conditions found underneath shears in scrap processing operations.
The Customer
Leading supplier of pipes, casing and tubing.
The Challenge
The EPC contractor turned to Magaldi for a dependable solution to automatically convey both chips and scrap generated during the finishing process.
The Solution
Magaldi supplied 5 Superbelt® conveyors to evacuate scrap and chips from the shear machines.
Installed in a pit, 4 conveyors are equipped with a specifically designed loading chute. The pans are in Hardox 400 to resist wear and heavy impacts as the material can sometimes come in clusters. A centralized lubrication system is installed on the conveyors to allow constant lubrication of both idlers and drums bearings.
The fifth Superbelt® handles the material coming from a water cutting machine. Due to the presence of water, pans and mesh belt are made of stainless steel.