The MAC® system
(Magaldi Ash Cooler)
A patented system for dry extraction, air cooling, and mechanical handling of bottom ash from pulverized coal-fired boilers
Due to growing concerns about water scarcity and ever-tightening environmental regulations, coal-fired power plants are switching to dry ash handling technologies.
With 200+ dry bottom ash handling systems installed worldwide since 1985 for both new boilers and retrofits, Magaldi is uniquely placed in the dry ash handling field to demonstrate the benefits of its MAC® system over wet ash handling systems.
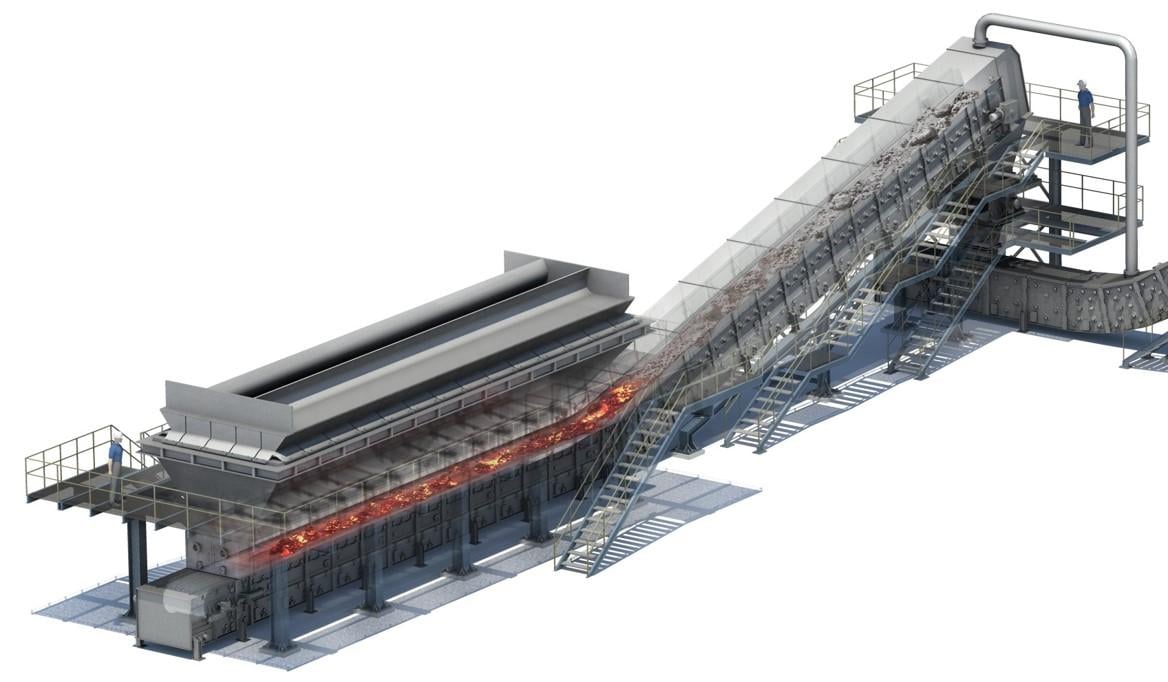
Dry vs. Wet
Unlike conventional wet bottom ash handling (WBAH) systems, responsible for huge water consumption, high maintenance costs, environmental issues, and negative effects on boiler operation, the MAC® (dry bottom ash handling) system delivers a reliable, cost-effective, and environmentally friendly operation thanks to the unique combination of the dry cooling process and the dependable Superbelt® conveying technology.
Water & cost savings
The use of the dry bottom ash handling (MAC®) system leads to significant water savings.
Since no water is used for ash cooling and conveying, all ancillary equipment/systems (pumps, piping, dewatering bins, water treatment plants, etc.), which are mandatory for WBAH systems, are no longer necessary, and therefore all associated O&M costs are eliminated.
Water consumption is limited to a minimum, only for dust control at the final discharge point. The water rate is strictly controlled when used for dust dispersion purposes.
Reduced disposal costs &
Increased ash marketability
The implementation of the MAC® system also reduces ash disposal costs. The limited amount of water cuts back on the landfilling cost due to the significant reduction in ash weight.
As a gainful alternative to landfilling, milled bottom ash can be sold to the cement industry since its features (dry and with lower unburned content) increase its saleability.
Increase in boiler efficiency &
Environmental risks mitigation
The installation of the MAC® system provides an increase in boiler efficiency within the range of 0.1÷0.6% (calculated within the framework of ASME PTC4), depending on actual coal properties and ash rates.
Much of the heat leaving the steam generator through the lower opening (radiant flux from the furnace, sensible heat, and the chemical energy contained in bottom ash due to its unburned carbon content) is recovered back by the cooling air which has become hot.
The increase in boiler efficiency also results in lower coal consumption which, in turn, reduces CO2 emissions and ensures effective environmental risk mitigation.
Additional cooling &
transport to the final delivery point
Typical MAC® system configuration includes the Magaldi Postcooler (Ecobelt®) downstream of the crushing stage. It is a secondary conveyor which provides further cooling while conveying bottom ash to the final delivery point.
Fully enclosed in a steel casing kept under slight negative pressure, the Ecobelt® conveyor features a self-cleaning system made of steel plates properly shaped and hinged to the belt. In the return part of the belt, the plates move the fines backward to the tail section, where the Magaldi O-chain® reloads them to the main belt.
The Superbelt® conveyor technology
Apart from the overall benefits of dry over the wet system, the MAC® system offers compelling benefits that derive from the use of the Superbelt® conveyor applied to dry ash handling, including:
- high dependability
- high temperature resistance
- high resistance to impact
- negligible wear and no tear issues
- low power demand
- low and easy maintenance
- weigh belt sections (as an option).
Some successful stories
Colombia
Dry bottom ash handling in a coal-fired power plant
Coal-fired power plant
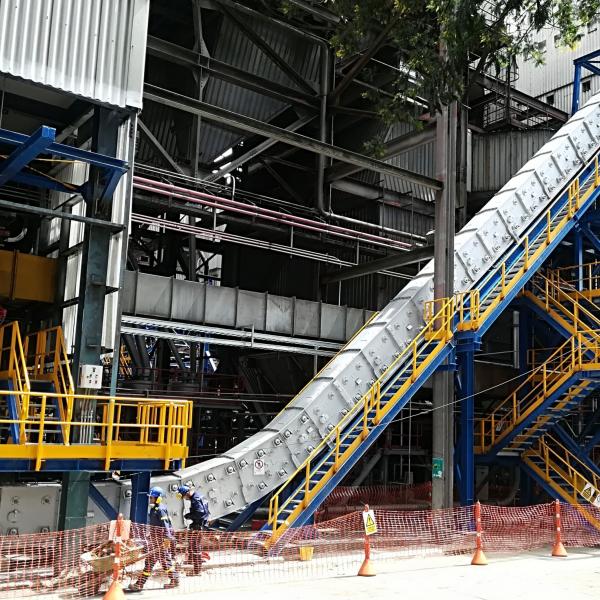
Magaldi Dry Bottom Ash Handling system is a dependable and environmentally friendly solution to face “El Niño” phenomenon.
The Customer
The Power Plant has a total installed generation capacity of 236 MWe: unit #2 is designed for a gross electrical output at a nominal load of 38 MWe while units #3, #4 and #5 have a gross electrical output of 66 MWe each. All generation units are based on a pulverized coal-fired (PC) boilers configuration.
The Challenge
In recent years, Colombia faced its most challenging energy crisis due to catastrophic effects procured by “El Niño” phenomenon, which led to extreme drought and undermined the stability of the Country’s energy supply. To cope with this emergency, the Customer decided to retrofit the existing wet system with a more dependable dry one.
The Solution
Four MAC® systems were installed under units #2, #3, #4 and #5 to increase the plant dependability and generate clean energy.
The first MAC® system is fully operational since July 2018, the second one was installed in September while the start-up for the remaining two systems was respectively performed in November 2018 and January 2019. Magaldi provided a turn-key solution for bottom ash removal, from the boiler terminal points up to the discharge into open trucks, including electrical equipment, steel support structures and the BA storage silo.
USA
Dry bottom ash handling in a coal-fired power plant
Coal-fired power plant
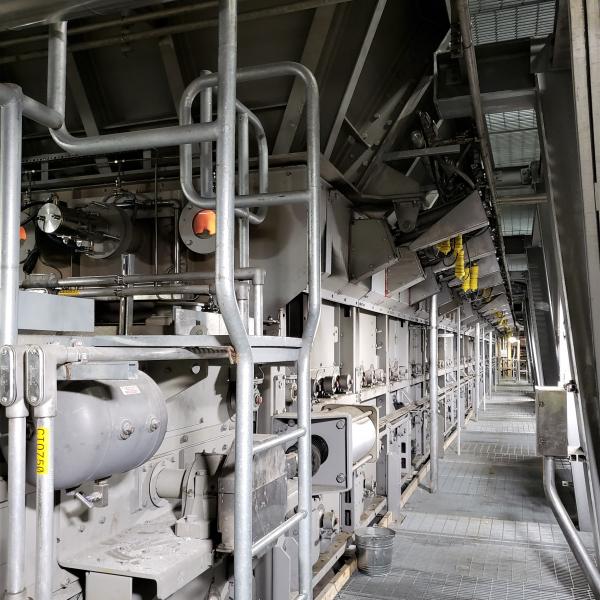
Magaldi dry technology was installed on all four units to meet EPA standards. It made the plant better from a safety, operations, maintenance, and housekeeping standpoint.
The Customer
With an installed generation capacity of nearly 3.600 MWe, the power plant is amongst the largest electricity generation facilities in the US, the largest power station fueled exclusively by coal.
The Challenge
The Customer needed to comply with environmental regulations (CCR/ELG) imposing new standards to limit water and ash ponds use.
The Solution
The MAC® system allowed to overcome all water-related problems – both operational and environmental – associated with dewatering bins, wastewater treatment, pumps, heat exchangers or pH control corrosion, water leakages, hot water splashing or vapor explosion, risk of ice in cold climates, pollution from ponds and so on.
Additionally, it proved to be less maintenance intensive than any other technology on the market.
Japan
Dry bottom ash handling in a coal-fired power plant
Coal-fired power plant

test
The Customer
One of the world’s most efficient coal-fired power plants. Magaldi received the order to install its dry ash handling system on Unit #3 (600 MWe).
The Challenge
After the Fukushima Daiichi nuclear disaster, all Japanese nuclear power plants were closed for safety reasons. This decision led to an increase in the consumption of fossil fuels and consequently to a wave of new green coal plant constructions.
Along with its Japanese licensee Kawasaki Heavy Industries (KHI), Magaldi took part in this "coal spring".
The Solution
Magaldi was responsible for the system from design and manufacture to equipment procurement and installation.
The ash handling system is installed on Unit 3, which is being added to the Thermal Power Plant to output 600 MW of power. The system is composed of a subsystem to handle fly ash (flying ash in exhaust gas) captured by an electrostatic precipitator and a subsystem to handle bottom ash (also known as clinker ash) from the bottom of the furnace. Bottom ash is dry-treated. The old wet handling method used water to cool and transport bottom ash, which was then dewatered and carried to the ash disposal site by truck or some other method. In contrast, the dry handling method uses air to cool the bottom ash while it is being transported dry. This decreases environmental impact, reduces costs, and saves space by eliminating the need for equipment such as for water supply, wastewater treatment, dewatering, and water storage. It also increases boiler efficiency and saves energy such as by enabling recovery of sensible heat from bottom ash, reaction heat from unburned carbon, and radiant heat from the furnace.