The Ecobelt® conveyor
Reduced material handling cycle time and the lowest temperature drop of the transported material for a more efficient and cost-effective downstream remelting process
Secondary aluminum smelting turns aluminum scrap into aluminum that can be used and recycled repeatedly in a closed-loop process.
It offers environmental and economic benefits in terms of reduced landfill waste, greenhouse gas emissions, and energy consumption (recycling a ton of aluminum requires only 5% of the energy used to refine primary aluminum from bauxite ore), thus making the secondary aluminum environmentally sound and economically viable.
Because aluminum scrap comes from various sources, the presence of impurities requires preliminary operations and treatments (including sorting, comminution, and thermal treatments) to improve the scrap quality in terms of metal yield and recyclability.
In particular, the ability to decoat aluminum, typically through a rotary kiln, improves the process by reducing metal losses and allowing the use of a broader range of scrap.
Magaldi tailored its conveyor technology to support the decoating process. Specifically, the Ecobelt® conveyor is designed to transport hot shredded scrap from the decoating kiln to the melting furnace. In the case of multiple furnaces, the integrated flow rate detection system determines the total shared rate and distributes it to each served furnace through a special diverter valve.
High reliability
The Ecobelt® conveyor features partially overlapping steel pans securely bolted on a patented steel double-wire mesh system.
The pans are provided with transversal cleats to keep material on the belt when traveling along inclines.
The belt damage-tolerant design is based on a multi-link concept: the mesh ensures redundancy, little to no maintenance, and trouble-free continuous operation. Even in case the mesh gets severely damaged, the conveyor will keep running without sudden failures till the scheduled maintenance.
The trouble-free operation ensures productivity and profitability and results in greater efficiency and uptime during a 24/7, year-round process.
High temperature resistance
The temperature of the shredded scrap at the kiln discharge is in the range of 500-600 °C. A heat-resistant conveyor is, therefore, paramount to ensure safe and reliable transport.
With the Ecobelt® conveyor, high temperatures and tear issues are solved thanks to the patented method of connecting the pans to the mesh belt, which leaves all elements free to thermally expand in any direction without permanent deformation. As a result, the conveyor is able to withstand temperatures of up to 1,100°C.
Reduced dust emissions &
low temperature drop
The Ecobelt® conveyor is fully enclosed in a steel casing that minimizes dust emissions and ensures the lowest temperature drop of transported material. This means that aluminum shreds can be charged into the melting furnace while still hot, thus allowing to reduce the required melting time while saving energy.
Very quiet operation
With the Ecobelt® conveyor, the smooth running without vibrations and the fully enclosed design reduce noise emissions considerably. The noise level is generally below 75 dB(A), less than half as loud as conventional conveyors with chains.
Low & easy maintenance
Downtimes and maintenance costs have been reduced in all cases where Ecobelt® conveyors have replaced conventional material handling systems.
The absence of chains, pinions, wear bars, and sprockets positively affect the belt conveyor wear rate and slash O&M costs to the bone.
Also, as uptime is a critical factor for any conveyor, the Ecobelt® has been designed to allow a quick replacement of key components despite the enclosed environment. All bearings are installed in a clean and cold area outside the casing, allowing trouble-free maintenance and lubrication with the belt running.
Some successful stories
Germany
Hot shredded scrap conveying
Aluminum recycling plant
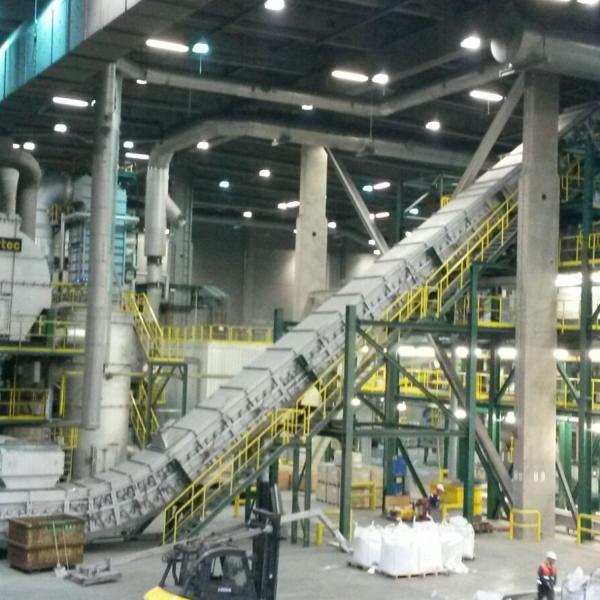
Thanks to the improved sealing, the Ecobelt® conveyors drastically reduced heat losses. Thermal energy released from the upstream processes is reused in the melting process.
The Customer
World’s largest and most technologically advanced aluminum recycling center, processing up to 400,000 tons of scrap annually.
The Challenge
The apron conveyors used to move hot shreds from the rotary de-coaters to the melting furnaces were extremely high in maintenance because bushings and chain links – directly exposed to high temperature and dusty material – needed frequent greasing. Additionally, the existing conveyors caused significant heat dispersion, and the resulting heat losses made the process less efficient. The customer definitely needed to find a better solution.
The Solution
Magaldi agreed to simulate the operating conditions of the plant to better customize the solution. Eight Ecobelt® conveyors serve the Can and the Flex lines transporting hot (550°C) aluminum shreds from the rotary de-coaters to the downstream melting furnaces. The conveyors work on 3 shifts, under high temperatures and severe conditions, guaranteeing the reliability of 98% and the lowest temperature drop.
USA
Hot shredded scrap conveying
Aluminum recycling plant
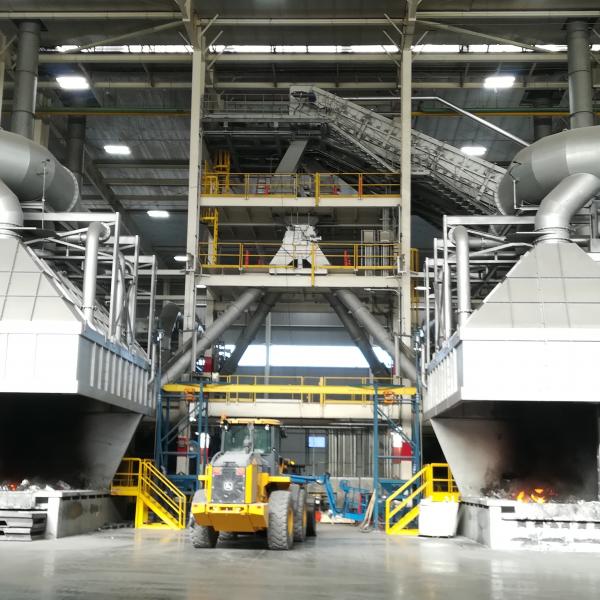
Maintenance efforts have been reduced. The plant is faced with fewer operating expenses and less downtime.
The Customer
Aluminum recycling facility manufacturing flat rolled aluminum sheets for the beverage can market.
The Challenge
The facility was experiencing breakdown after breakdown. The attempt to use an apron conveyor to handle hot aluminum shreds had proven to be unsuccessful due to the frequent stops to repair broken chains.
The Solution
Four Ecobelt® conveyors were installed to connect the delacquering kilns with the downstream furnaces, transporting up to 20 t/h of aluminum shreds at about 580°C. Unlike the apron conveyors, the Ecobelt® ensured high availability and reliability, providing greater assurance of uptime and reduced maintenance. Additionally, the capability to reduce the temperature drop positively affected the performance of the downstream furnaces, reducing the energy consumption.