The FLUIMAC® system
A patented system for dry handling of Bed Ash from Fluidized Bed Combustion (FBC) boilers
Due to the major advantages over PC boilers, the use of FBC boilers has grown rapidly as well as their capacity. This required not only boiler technology but also auxiliary system improvements.
One of the critical auxiliary systems of FBC boilers is the bed ash extraction system, which must be capable of removing and cooling hot and abrasive materials of different sizes.
Based on its field-proven MAC® technology for PC boilers, Magaldi has developed the FLUIMAC® system.
Dry vs. conventional systems
Unlike conventional bed ash extraction systems, responsible for huge water consumption, high maintenance costs, environmental issues, and negative effects on boiler operation, the FLUIMAC® dry system delivers a reliable, cost-effective, and environmentally friendly operation thanks to the unique combination of the dry cooling process and the dependable Superbelt® conveyor.
Water & related costs savings
The use of the dry bed ash handling system results in significant water and O&M cost savings.
Since no water is used for ash cooling and conveying, water circulation and treatment systems are no longer necessary, and the associated costs are eliminated.
The absence of water also cuts maintenance costs arising from corrosion and jamming along the sluicing line and creates a cleaner and safer work environment.
Increase in boiler efficiency &
Environmental risks mitigation
Unlike conventional wet systems, where the increase in water temperature is generally low so that energy cannot be recovered profitably, the FLUIMAC® stands out for a high potential recoverable heat from the ash. Hot air can be delivered to the secondary air (SA) duct by a dedicated fan, allowing for consequent heat recovery to the boiler, or to a negative pressure point in the boiler circuit.
The increase in boiler efficiency also results in lower coal consumption which, in turn, reduces CO2 emissions and ensures effective environmental risk mitigation.
No mechanical wear
Because of the small size, physical hardness, and sharp edges of its particles, bed ash is a very abrasive material. Conventional methods to remove and cool hot bed ash from FBC boilers undergo mechanical wear, leading to high maintenance costs.
With the FLUIMAC® system, ash is extracted and transported by the Superbelt® (steel belt), designed to avoid sliding friction between any moving part of the belt and the transported material. It helps keep the wear to negligible levels, so much so that the expected life of the belt is 10+ years.
High reliability
The FLUIMAC® system also delivers additional benefits that derive from the use of the Superbelt® applied to dry handling of bed ash.
The Superbelt® smoothly extracts bed ash through a distributing device installed below each drain pipe and continuously conveys it while ensuring the highest dependability. The multi-link design of the mesh belt guarantees continuous trouble-free operation, avoiding unexpected failures.
High temperature resistance
Regarding high temperature resistance, the patented method of connecting the pans to the mesh belt leaves all elements free to thermally expand in any direction, without permanent deformations. Hence, the conveyor withstands temperatures higher than any other known competing technology.
Fuel flexibility
The main advantage of using FBC boilers is the ability to burn a wide range of fuels. However, fuel variation implies a change in bed ash particle size, which can seriously affect the operation of the bed ash handling system.
Unlike competing technologies, the FLUIMAC® extractor is able to safely transport bed ash of various sizes, whether they contain big lumps or not, due to the Superbelt® unique design. This feature gains the FLUIMAC® a key competitive advantage since it allows for greater fuel flexibility.
Additional cooling &
reliable transport to the final delivery point
Typical FLUIMAC® system configuration includes the Ecobelt® conveyor (Magaldi Postcooler): a secondary conveyor which provides further cooling while conveying bed ash to the final delivery point.
Fully enclosed in a steel casing kept under slight negative pressure, the Magaldi Postcooler features a self-cleaning system made of steel plates properly shaped and hinged to the belt. In the return part of the belt, the plates move the fines backward to the tail section where the Magaldi O-chain® - a cleaning chain enclosed in an independent carter - reloads them to the main belt.
The Magaldi Postcooler can also be installed downstream of alternative types of Bed Ash extraction and cooling equipment, such as screw coolers, rotary drum coolers, etc..
Some successful stories
India
Fluidized bed ash handling
Coal-fired power plant
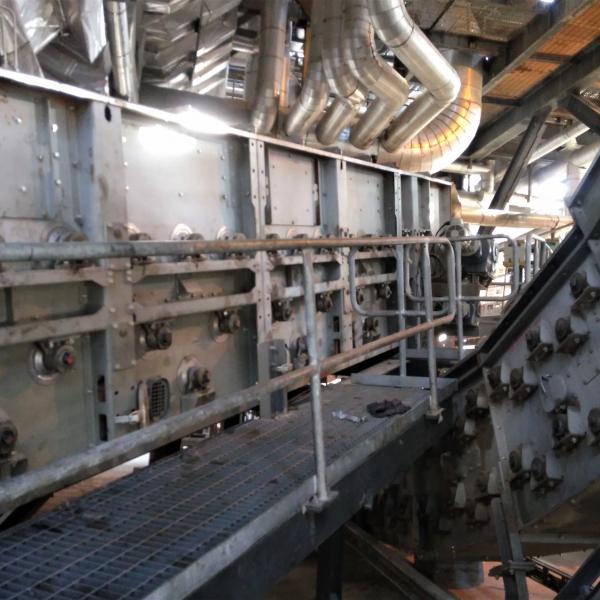
The FLUIMAC® allowed overcoming the critical aspects of conventional bed ash systems.
The Customer
Captive power plant (2x300 TPH CFB coal/pet-coke fired steam generators).
The Challenge
In 2015, the EPC company selected Magaldi for the supply of 2 FLUIMAC® systems to handle the bed ash produced by the CFB boilers.
The Solution
The FLUIMAC® extractors receive the bed ash at high temperatures from the drain pipes, thus exercising a double function:
- cooling the ash by the ambient air flowing in the system. No water is required;
- conveying the ash to the downstream equipment.
The FLUIMAC® allowed overcoming the critical aspects of conventional bed ash systems (e.g. screw coolers, rotary drums, fluidized bed coolers) while ensuring:
- No wear due to friction between ash and belt (no relative movement);
- No water consumption (the cooling medium is only ambient air);
- No risk of water leakages;
- No risk of unexpected failures;
- Smooth handling of ash particles of different sizes;
- Recovery of the ash sensible heat.
South Korea
Fluidized bed ash handling
Coal-fired power plant
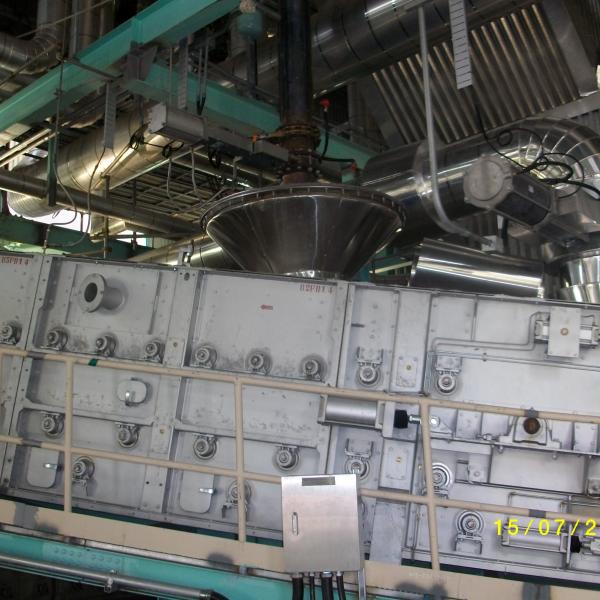
The FLUIMAC® systems contributed to increasing the boiler performance by recovering heat back to the combustion chamber, reducing the coal consumption, and eliminating the water used to cool down the bed ash, all fully in line with the advantages given by the boiler.
The Customer
The coal-fired power plant has a total installed capacity of 680 MW.
The Challenge
In 2007 a fuel conversion project was aimed at switching from heavy oil combustion to state-of-the-art environmentally friendly facilities based on fluidized bed boilers. Considering these expectations, the installation of the FLUIMAC® systems was a natural choice.
The two greenfields started commercial operation in 2011 (Unit #2) and 2016 (Unit #1). Thanks to eco-friendly circulating fluidized bed boilers using low-grade coals, the thermal power plant significantly cut fuel costs and remarkably reduced greenhouse gas emissions, such as nitrogen and sulfur oxides.
The Solution
For each unit, Magaldi designed and supplied a dry system to transport bed ash from the boiler drain pipes to the storage silo, bringing together all of the latest innovations to ensure good performance under any operating condition.
Due to different operating pressures between the CFB boiler and the FLUIMAC® system, it was necessary to keep them separate by maintaining the boiler drain pipes always full of ash and continuously regulating the speed of the FLUIMAC® extractors according to the actual bed ash production. The hot bed ash flowing down through the drain pipes is uniformly distributed over the extractors and then discharged to the Ecobelt® conveyor for further transportation to the bucket elevator before loading into the storage silo. During transport, the bed ash is cooled by a counter-current airflow and drafted into the FLUIMAC® system by unique fans for air treatment. Located downstream of the Ecobelt® discharge chute and upstream of the bucket elevator, the Contact Cooler® assures an effective drop of the bed ash temperature since it brings into direct contact the falling ash and the fresh air entering the equipment from below. The cooling air circulation and its continuous rate adjustment, necessary to achieve effective ash cooling and to maximize the heat recovery to the boiler, is guaranteed through the special air fans. Two cyclones reduce the dust content and avoid corrosion problems in the air ducts.