The Ecobelt® conveyor
Ideal for transporting hot and abrasive sinter, both in iron and steelmaking plants and in primary metallurgical processes
Sinter plants must run at peak performance to successfully produce under high-cost pressure. It means no equipment failures or costly material break-ups can occur.
That is why more sinter plants are breaking with conventional solutions (rubber belts, vibratory or apron-based conveyors) in favor of a more reliable way to transport sinter.
Thanks to its excellent heat and abrasion resistance features, the Ecobelt® conveyor is used to move sinter lumps, at very high temperatures, from the primary crusher to the rotary cooler, or it can be installed at the cooler discharge for further transport if the material is still too hot for rubber belt conveyors.
High reliability
The Ecobelt® conveyor features partially overlapping steel pans securely bolted on a patented steel double-wire mesh system.
The pans are provided with transversal cleats to keep material on the belt when traveling along inclines.
The belt damage-tolerant design is based on a multi-link concept: the mesh provides redundancy, little to no maintenance, and trouble-free continuous operation. Even in case the mesh gets severely damaged, the conveyor will keep running without sudden failures till the scheduled maintenance.
The trouble-free operation ensures productivity and profitability and results in greater efficiency and uptime during a 24/7, year-round process.
High temperature resistance
High temperatures experienced when transporting sinter place serious problems on both rubber and chain conveyors. They cause burning and accelerated aging of rubber belts, which must be replaced more and more often. The cost for the belt replacement is just one aspect of the matter. A more important consideration is the cost of downtime in manufacturing. Hence, even if comparatively inexpensive to purchase, rubber belt conveyors have considerably high operating costs.
Chain conveyors also suffer from high temperatures that, applied over long periods, cause subcritical annealing of conveyor parts. Thermo-mechanical fatigue can lead to a significant decrease in the hardness of both chains and wheels.
With the Ecobelt® conveyor, high temperatures and tear issues are solved thanks to the patented method of connecting the pans to the mesh belt, which leaves all elements free to thermally expand in any direction without permanent deformation. The result is a heat-resistant conveyor able to withstand temperatures up to 1,100°C.
Reduced dust emissions
Sinter transportation may give rise to airborne dust, exposing plant operators to health and safety hazards.
Due to their very nature, vibratory conveyors are not a good solution as vibration can cause dust formation.
Conversely, the completely enclosed design of the Ecobelt® conveyor eliminates all dust emissions. Additionally, the smooth running without vibrations and the overlapping design of the steel pans prevent the formation of fine particles otherwise produced by vibration conveying, leading to increased productivity at lower costs (no need for added clean-up).
Any fine residual that may drop off the conveyor is removed by a simple mechanical self-cleaning device made of dragging buckets that scrape the bottom of the casing and push the fines up to the Magaldi O-chain®. The latter is a chain conveyor enclosed in an independent casing tailored around the Ecobelt® tail section, whose job is to bring the recovered fines back to the carrying side of the belt.
High-quality sinter
The transport mode affects the quality of the sintered material as well.
With the Ecobelt®, since the conveying is vibration-free, neither aging nor chemical changes of the sinter are caused. Also, the smooth transport creates fewer cracks with the sinter, thus preserving its structural integrity. The result is a high-quality material, whose high reducibility decreases the intensity of blast furnace operations and the coke demand.
Negligible wear
Sinter is a very abrasive material acting as a micro-tool that, over time, abrades the surfaces on which it slides.
With the Ecobelt® conveyor, wear is negligible because there is no relative motion between the moving parts. Thus, the operator is faced with fewer operating expenses and less downtime.
Low & easy maintenance
In all cases where Ecobelt® conveyors replaced conventional material handling systems, downtimes and costs for maintenance have been reduced.
The absence of chains, pinions, wear bars, and sprockets positively affects the belt conveyor wear rate and slashes O&M costs to the bone.
Also, as uptime is a critical factor for any conveyor, the Ecobelt® has been designed to allow a quick replacement of key parts despite the enclosed environment.
Some successful stories
Brazil
Hot sinter conveying
Sinter plant
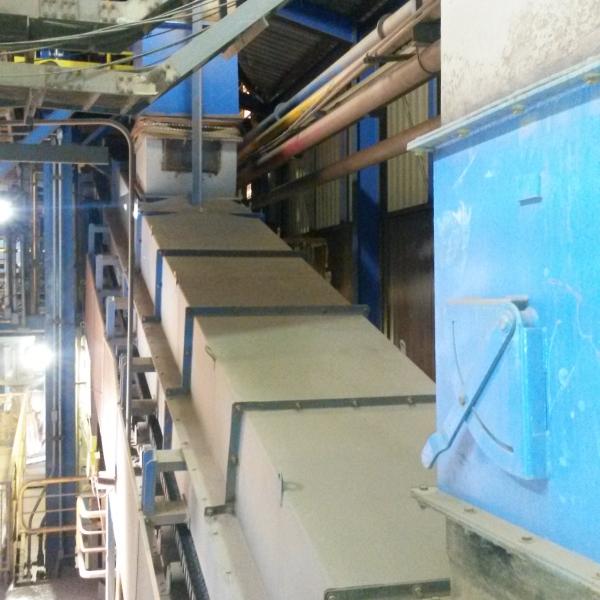
The Ecobelt® conveyor is an environmentally friendly solution to minimize fugitive dust, material spillage, and the associated risks to operators and the environment.
The Customer
Premium supplier of niobium products.
The Challenge
Provide a reliable solution for dust-free transport of hot and abrasive sinter material.
The Solution
Downstream the sintering car a crusher crumbles sinter lumps and discharges them on a Superbelt® conveyor. The latter transports approx. 70 t/h of sintered material at 300°C, with peaks of up to 500-550°C.
Placed orthogonally to the first conveyor, an Ecobelt® receives the material and transports it to a rubber belt. To protect the downstream rubber belt from high temperatures, the Ecobelt® features a cover with air intake points to cool the hot sinter.