The Superbelt® conveyor
Designed to move forged parts at extreme temperatures
Magaldi’s hot forging conveyors are extremely versatile and can be used for transporting pieces in a wide range of sizes and shapes, at their very highest temperature.
High reliability
The Superbelt® conveyor features partially overlapping steel pans securely bolted on a patented steel double-wire mesh system.
The belt damage-tolerant design is based on a multi-link concept which ensures redundancy, little to no maintenance, and trouble-free continuous operation. Even in case the mesh gets severely damaged, the conveyor will keep running without sudden failures till the scheduled maintenance.
The trouble-free operation ensures productivity and profitability and results in greater efficiency and uptime during a 24/7, year-round process.
High temperature resistance
Forging operations can be brutal on conveying equipment. The high temperatures experienced when transporting glowing red forged parts place demands on conveyor belts.
With the Superbelt® conveyor, all issues related to high temperature resistance are solved thanks to the patented method of connecting the pans to the mesh belt, which leaves all components to freely expand in any direction without permanent deformations. The result is a conveyor able to carefully transport components at temperatures of up to 1100 °C.
Unique discharge chute for reduced damage to forged parts
Smooth running is key to reducing the risk of damaging forged parts during transport.
To further preserve the quality of the forged parts even during the transfer stage, Magaldi designed, developed, and tested a new discharge chute featuring a unique “sandwich” design that reduces both the shock impact loads and the resulting noise.
Little to no maintenance
The Superbelt® conveyor requires little to no maintenance as it is devoid of critical wear points (no wear bars, pins, hinges, chains, or sprockets). The only points requiring lubrication are the head and tail pulley bearings, which can be greased with the belt running. The other components are designed for continuous operation and can be checked during preventive maintenance over a multi-year schedule.
Some successful stories
Spain
Hot forged parts conveying
Forging plant
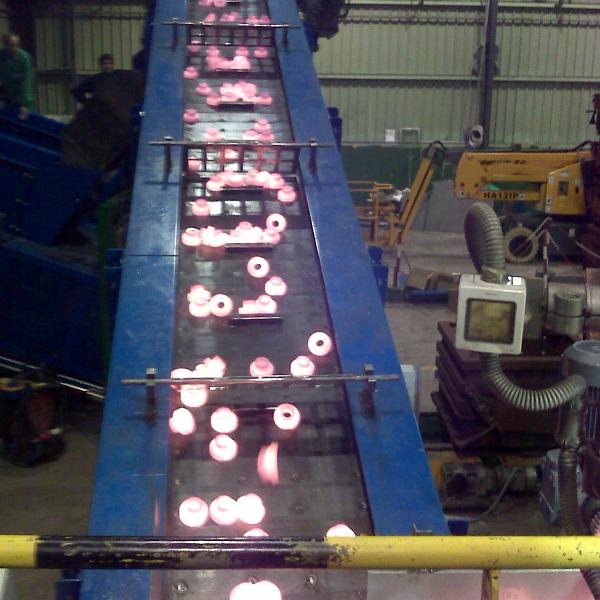
Eight small Superbelt® conveyors made it possible to reliably move the hot forged parts (800°C) along the production line.
The Customer
Manufacturer of components for the automotive sector focused on the Hatebur forging technology.
The Challenge
To reliably transport forged parts at a temperature of 800 ° C.
The Solution
Magaldi supplied eight small Superbelt® conveyors to handle hot forged parts within the plant.
At the press discharge, a Superbelt® conveyor discharges the forged parts onto two parallel Superbelt® conveyors, pending the downstream annealing process.
Installed along the line that includes the heat treatment furnace and the cooler, three additional Superbelt® conveyors handle the material in a controlled environment to secure its proper hardness and metallurgical properties.
Downstream the cooler, another Superbelt® discharges the pieces into bins while the last Superbelt® loads the shot blasting machine for subsequent processing.