Magaldi Casting Cooler
(MCC®)
Raffreddamento controllato dei getti e ridotte emissioni di silice cristallina respirabile
Uno degli aspetti più importanti ai fini della produzione di getti di alta qualità è l’efficienza del processo di raffreddamento, determinata dal tempo di residenza delle fusioni all’interno del tunnel. Il tempo di raffreddamento varia a seconda dei volumi di produzione, delle dimensioni del getto, degli spazi disponibili e di altri fattori non controllabili. Un sistema flessibile, in grado di controllare il processo di raffreddamento ed adattarsi alle specifiche esigenze di produzione è, dunque, la chiave del successo.
Generalmente installato tra la shakeout e la granigliatrice, l'MCC® è composto da:
- il trasportatore a nastro Superbelt®, che ne costituisce il componente chiave e assicura elevata affidabilità, manutenzione minima e un funzionamento continuo senza problemi.
- Un tunnel di raffreddamento tenuto in pressione negativa.
Un flusso d'aria ambiente entra attraverso le estremità del tunnel ed esce attraverso la cappa centrale. L'aria di raffreddamento fluisce a velocità controllata sui getti per raffreddarli fino alla temperatura desiderata, evitando shock termici e/o altri difetti microstrutturali.
Design robusto
I sistemi di raffreddamento sono chiamati a funzionare in condizioni operative difficili dovute alle alte temperature del materiale trasportato, alla presenza di terra e al carattere abrasivo dei getti.
Grazie alla tecnologia di trasporto Superbelt®, Il raffreddatore MCC® è in grado di resistere all’usura di materiali estremamente abrasivi e di sopportare temperature superiori a qualsiasi altra tecnologia concorrente. Il metodo brevettato di collegamento delle piastre al nastro lascia tutti i componenti liberi di espandersi in qualsiasi direzione senza deformazioni permanenti mentre il sistema di tensionamento compensa automaticamente le dilatazioni termiche. Ne risulta una capacità di resistere a temperature fino a 1100C.
L’assenza di moto relativo tra il materiale trasportato e le parti metalliche del trasportatore riduce, invece, notevolmente l’usura e lo rende meno sensibile al carattere abrasivo del materiale trasportato.
Processo di raffreddamento ingegnerizzato
Per ogni singolo progetto, Magaldi studia a fondo le proprietà sia dell'aria di raffreddamento che dei getti, per definire i parametri di processo più efficaci.
L'uso combinato di metodi analitici (es. analisi CFD), test sperimentali e misurazioni sul campo hanno consentito di creare e testare modelli termodinamici molto accurati, grazie ai quali siamo in grado di assicurare un processo di raffreddamento ottimizzato.
Raffreddamento ad aria controllato
Uno dei fattori più critici nel processo di raffreddamento delle fusioni è il metodo di scambio termico adottato.
Il raffreddatore MCC® utilizza in combinazione flussi d'aria in parallelo e in controcorrente. Il risultato è un gradiente di temperatura più basso all'ingresso del tunnel di raffreddamento, per cui lo stress termico nei getti è ridotto mentre l'efficienza complessiva del processo è massimizzata.
Efficace raffreddamento anche in spazi ridotti
In caso di spazi ridotti, è possibile utilizzare un ulteriore flusso d'aria (cross-flow) che aumenta l’efficienza del processo di raffreddamento.
Con il raffreddatore SuperMCC®, un terzo flusso d'aria entra nel sistema attraverso fori appositamente realizzati sulle piastre del nastro. L'aria di raffreddamento non solo scorre intorno alle fusioni ma passa anche sotto e tra di loro. Una parte più ampia della superficie dei getti è esposta all’aria e, dunque, si raffredda più velocemente.
Sistema Integrato di Supervisione (MISS®)
Una fase di messa a punto e regolazione dei parametri di raffreddamento è fondamentale per un processo che sia affidabile e flessibile. Per tale ragione, il raffreddatore MCC® può essere dotato di un sistema integrato di supervisione (MISS®), che effettua un controllo dinamico sui parametri di processo in funzione delle diverse tipologie di fusioni da raffreddare.
Collegato ai segnali operativi della linea di formatura a monte, il MISS® riceve il numero identificativo (ID) di ogni getto e la temperatura effettiva rilevata da pirometri ottici situati lungo il tunnel di raffreddamento. A seconda dei parametri sopra indicati, il sistema regola automaticamente la velocità del nastro e la portata dell'aria di raffreddamento, massimizzando così l’efficienza del processo di raffreddamento.
Ridotte emissioni di silice cristallina respirabile
Il raffreddatore MCC® offre un vantaggio competitivo nella gestione di un problema molto delicato qual è la sovraesposizione dei lavoratori alla polvere di silice cristallina. Il trasporto delicato e senza vibrazioni riduce, infatti, le emissioni di polveri, contribuendo ad un ambiente di lavoro più salubre e sicuro.
Basso consumo energetico
Grazie all’impiego del trasportatore Superbelt®, l’MCC gode di un basso consumo energetico (circa un decimo rispetto ai trasportatori vibranti). L’assenza di movimento relativo tra il materiale trasportato e le parti metalliche del nastro riduce drasticamente l’usura e la quantità di energia necessaria per il trasporto delle fusioni.
Raffreddamento, smaterozzatura e
cernita delle fusioni
Il trasporto lento, delicato e silenzioso (<75 dBA) consente agli operatori di utilizzare la lunghezza scoperta del nastro a valle del tunnel di raffreddamento come stazione di lavoro per la smaterozzatura (anche a mezzo di martelli, cunei idraulici, manipolatori o robot) e la cernita delle fusioni, evitando il ricorso ad ulteriori piani di lavoro.
Alcune storie di successo
Slovenia
Raffreddamento fusioni
Fonderia di ghisa
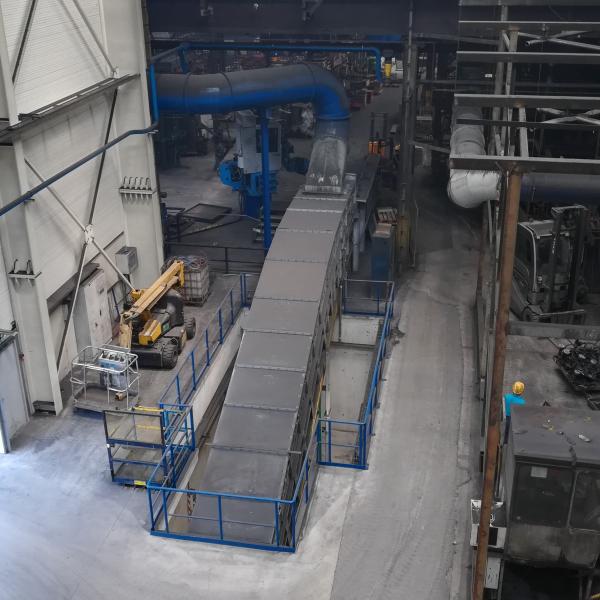
Controllo ottimale dei parametri di raffreddamento grazie al sistema MISS®
Il Cliente
Azienda leader nella produzione di componenti in ghisa sferoidale e grigia per l’industria ferroviaria.
La Sfida
L'obiettivo per la fonderia era raffreddare fusioni di grandi dimensioni e peso elevato, caratterizzate da alte temperature e un alto modulo termico.
La Soluzione
Gli ingegneri Magaldi hanno condotto test specifici per validare le curve di raffreddamento ottenute con codici di simulazione proprietari. Il risultato è stato un trasportatore MCC® in grado di raffreddare fusioni pesanti (fino a 633 kg) e di grandi dimensioni provenienti dalla linea di scuotimento a forma di “L”, portandole da 700°C a 70°C.
Italia
Raffreddamento fusioni
Fonderia di ghisa
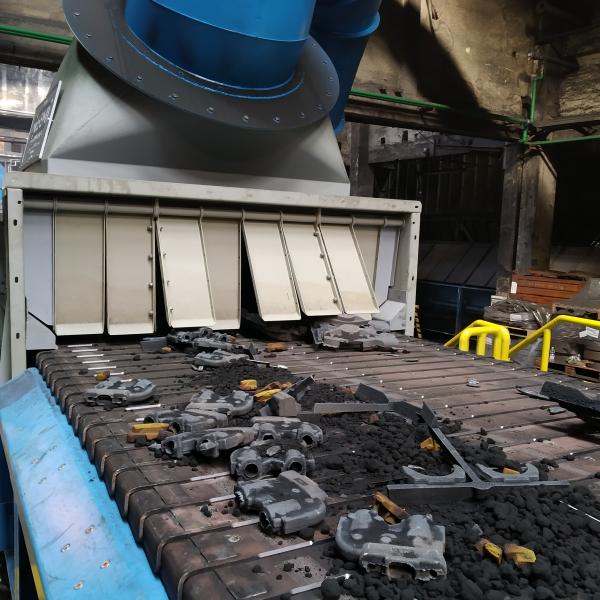
Processo di raffreddamento controllato per produzioni ad alto volume.
Il Cliente
La fonderia produce getti in ghisa grigia e sferoidale per diversi settori industriali.
La Sfida
Nell'ambito di un progetto di ammodernamento delle linee verticali DISA, il Cliente si è rivolto alla Magaldi alla ricerca di una soluzione integrata per il raffreddamento e la smaterozzatura dei getti che dalla zona di distaffatura sono trasferiti alla granigliatrice.
La Soluzione
Dopo la fase di distaffatura/sterratura, 2 trasportatori vibranti scaricano i getti sul raffreddatore Magaldi disposto ortogonalmente.
Il lungo MCC® raffredda le fusioni in sincrono con le linee DISA a monte. All'uscita del tunnel di raffreddamento, gli operatori eseguono la cernita e la smaterozzatura dei getti sul tratto scoperto del nastro. Le materozze vengono, invece, scaricate in un sistema automatico di movimentazione dei cassoni posto in testata di trazione per il successivo trasferimento all'area di fusione.
P.R.C.
Raffreddamento fusioni
Fonderia di ghisa

Con l'installazione del raffreddatore Magaldi, il cliente ha ridotto il tasso di scarto delle fusioni e migliorato la qualità del prodotto finito.
Il Cliente
Moderna fonderia specializzata nella produzione di blocchi motore in ghisa.
La Sfida
Accrescere la qualità delle fusioni migliorando le prestazioni e l'efficacia del sistema di raffreddamento.
La Soluzione
A valle delle shakeout, 2 canali vibranti collettano le fusioni e le scaricano sui raffreddatori MCC® formando un unico tunnel di raffreddamento lungo 54m. All'interno del tunnel, un flusso continuo di 40 t/h di getti è portato da una temperatura di 450°C a 80°C. All'uscita del tunnel, la parte scoperta di nastro è utilizzata come postazione di lavoro per la cernita e la smaterozzatura delle fusioni a mezzo manipolatori.