The Superbelt® conveyor
Tailored solutions for moving even the most fragile castings from the die casting machines to the downstream decoring area
Smooth handling is often the main factor in assuring casting quality and secure productivity.
The Superbelt® conveyor is the recommended solution for the gentle and smooth transport of aluminum cast parts throughout the plant.
As extremely versatile, it can be used to move castings of different dimensions, shapes, and weights, for short or long runs, straight or inclines.
High reliability
The Superbelt® conveyor features partially overlapping steel pans securely bolted on a patented steel double-wire mesh system.
The belt damage-tolerant design is based on a multi-link concept: the mesh provides redundancy, little to no maintenance, and trouble-free continuous operation. Even in the case the mesh gets severely damaged, the conveyor will keep running without sudden failures till the scheduled maintenance.
The trouble-free operation ensures productivity and profitability and results in greater efficiency and uptime during a 24/7, year-round process.
Reduced silica dust emissions
The Superbelt® conveyor provides a competitive edge in dealing with a very sensitive issues, such as workers' exposure to crystalline silica dust.
The smooth running and the absence of vibrations ensure that silica is not being thrown into the air, greatly reducing any chances for silica exposure.
Unique discharge chute for reduced damage to cast parts
Smooth running is also key to reducing the risk of damaging cast parts during transport.
To further preserve the casting quality even during the transfer stage, Magaldi designed, developed, and tested a new discharge chute featuring a unique “sandwich” design that reduces both the shock impact loads and the resulting noise.
Very quiet operation
The smooth running of the Superbelt® conveyor also reduces noise emissions considerably. Generally below 75 dB(A), the noise is less than half as loud as conventional conveyors with chains, which is advantageous for both the employees and the environment.
Low power consumption &
Negligible wear
Designed to avoid sliding friction among the moving parts, the Superbelt® conveyor has a low power consumption (about one-tenth compared to vibratory conveyors).
Also, as castings are slowly transported, there is no relative motion, so wear is negligible.
Little to no maintenance
The Superbelt® conveyor requires little to no maintenance as it is devoid of critical wear points (no wear bars, pins, hinges, chains, or sprockets). The only points requiring lubrication are the head and tail pulley bearings, which can be greased with the belt running. The other components are designed for continuous operation and can be checked during preventive maintenance over a multi-year schedule.
Some successful stories
Germany
Aluminum casting conveying
Aluminum foundry
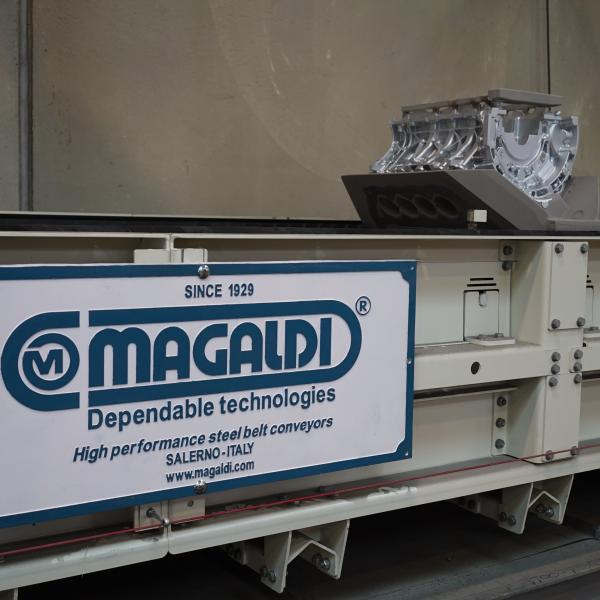
Uptime is a critical factor for any conveyor. The Superbelt® conveyor has been able to keep pace with the steadily increasing production.
The Customer
One of the world’s largest producers of light-metal components for the automotive industry. The foundry is dedicated to manufacturing large-volume components in mass serial production.
The Challenge
The Customer was looking for a conveyor which could keep pace with the short cycle times of the upstream high-pressure die-casting machines. Magaldi custom engineered a Superbelt® conveyor to handle the job.
The Solution
In 4 months Magaldi designed, produced, installed, and started up a Superbelt® conveyor that transports 15 t/h of aluminum engine blocks from 3 die-casting machines to the downstream decoring area. Providing greater uptime and ease of maintenance, the Superbelt® allowed for boosting foundry output and performance.