SMART - Magaldi High Performance Systems for the Cooling and Heat Treatment of Materials
Public Notice for the support to Campania enterprises in the implementation of feasibility studies (PHASE 1) and technology transfer projects (PHASE 2) consistent with RIS 3 - POR FESR CAMPANIA 2014/2020 - O.S.1.1 - Campania Region
Beneficiaries: Magaldi Power Spa
Term: 3 September 2018 - 30 November 2020
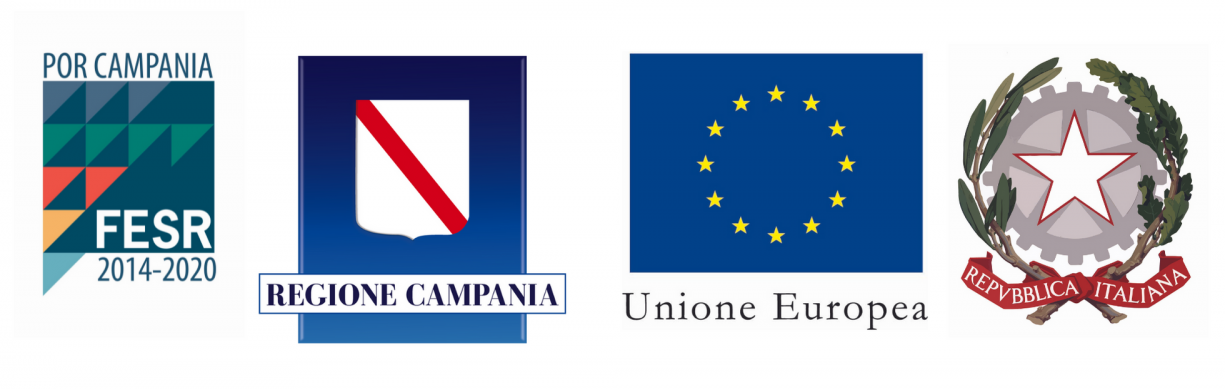
Based on the experience gained in the field and the knowledge acquired over the years, with the SMART project Magaldi has improved a technology capable of cooling both cast iron and aluminum castings, as well as optimizing the temperature control and more generally the cooling of reduced iron briquettes in order to address the market segment of raw material suppliers to steel mills.
The aims of the project were to study, realize and develop technologies for:
- the cooling of cast iron and aluminum castings;
- the transport of very hot materials, at high flow rates and characterized by plant configurations with significant geometric differences in height.
Within the SMART project, Magaldi Power has carried out industrial research and experimental development activities aimed at the design and construction of 3 pilot plants:
- Magaldi Casting Cooler (MCC®)
- Superbelt® High Speed (HS)
- Ecobelt® Bucket (ECO B)
The first prototype is a belt conveyor and cooler, named Magaldi Casting Cooler (MCC®), which is targeting the cast iron and aluminum foundry market.
In recent years, Magaldi has been increasingly dealing with this market and with the need to efficiently cool castings. In this context, a growing interest in foundries for metal belt cooling systems has been noticed. In accordance with market requirements, Magaldi has researched and developed customized solutions to optimize the casting cooling process. Specifically, the main features investigated to meet the needs of this market sector have been:
- Sizing and complete automation of the cooling system using air;
- Reducing the size of the components of the transport and cooling system, as well as the associated ventilation system, in order to adapt it to the reduced space available in the plant while maintaining the required thermal decay performance.
In fact, in some foundries, the installation of the casting cooling system requires space, which may be limited for several reasons: for instance, the compact configuration of the foundry, the size of the equipment around it, the type of castings that require long time spent inside the cooling tunnel and consequently a greater length of the tunnel, or simply a high molds/hour frequency and therefore a higher than usual belt speed with a consequently reduced time spent in the tunnel for the same length.
The other two belt conveyor prototypes, the Superbelt® High Speed (HS) and the Ecobelt® Bucket (ECO B), were initially designed for producers of iron briquettes, known as HBI, which stands for "Hot Briquetted Iron". Such briquettes, which are made from DRI pellets (the acronym stands for “Direct Reduced Iron”) are also used for other materials as listed below:
- HDRI pellets (Hot DRI);
- Fly ash from the combustion of coal, municipal solid waste, biomass in thermoelectric;
- Thermoelectric plants;
- Cement clinker;
- Foundry soils;
- Very fine and powdery materials in general, i.e. materials with an average particle size of less than 500 microns;
- Less than 500 microns on average.
Thus, the main fields of application are primary and secondary steelworks, cement works, foundries, thermoelectric power stations, and mineral raw material treatment and processing plants.