The Superbelt® conveyor
A worthy ally for safer, comfortable, and more efficient operations
Working on a conveyor line to degate and sort castings downstream the blasting process is a hard job and exposes workers to the risk of injuries when performed under a condition of repetitive vibrations, high noise levels, heavy lifting, and respirable dust.
For such a physically demanding activity, it makes sense to take every measure to reduce workers’ fatigue and boost their performance.
The unique design of the Superbelt® conveyor enables operators to sort finished castings more easily and comfortably, and allows for the use of hydraulic wedges, manipulators or robots directly on the belt for smoother production.
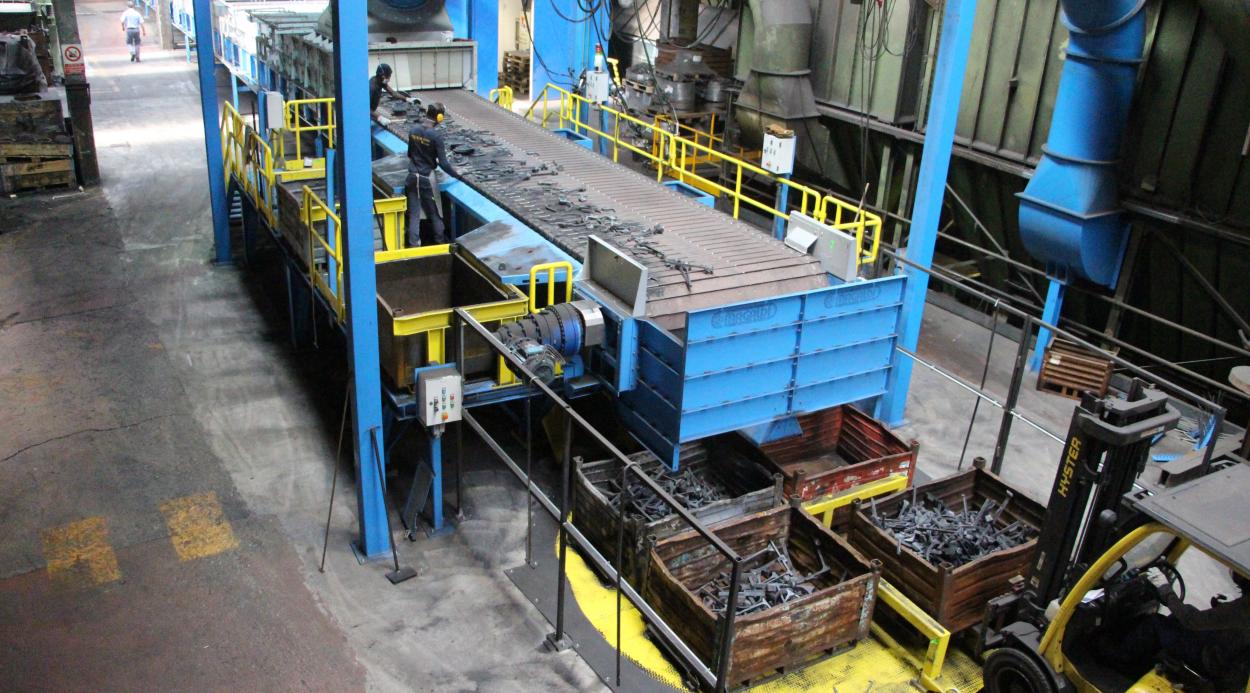
High reliability
The Superbelt® conveyor features partially overlapping steel pans securely bolted on a patented steel double-wire mesh system.
The belt damage-tolerant design is based on a multi-link concept: the mesh ensures redundancy, little to no maintenance, and trouble-free continuous operation. Even in the case it gets severely damaged, the conveyor will keep running till the scheduled maintenance, without sudden failures.
The trouble-free operation ensures productivity and profitability and results in greater efficiency and uptime during a 24/7, year-round process.
Impact toughness
The Superbelt® conveyor features specially designed carrying idlers, supports, and a heavy-duty shock absorber frame that make it suitable for demanding applications. As a result, the conveyor ensures high resistance to the impact loads coming from the degating tools (e.g. hammers, hydraulic wedges, manipulators, robots), which can be directly used on the belt without causing breakage or damage.
Greater safety &
ergonomics
The Superbelt® conveyors are designed to ensure safety & ergonomics.
The smooth running without vibrations, and the noise level below 75 dB(A), eliminate the risks of vibration-related injuries and reduce background noise.
Also, our conveyor solutions play a large role in developing ergonomic environments. Designed to be less labor-intensive, the Superbelt® can be used as a slowly-moving worktable that allows dragging castings towards the lateral chutes comfortably. There is no need for operators to stretch, pull and lift castings, thus minimizing strain injuries and increasing productivity.
Blast media recovery
When installed downstream of the shot-blasting machine, the Superbelt® conveyor can be equipped with a static unloading chute to separate and recover the blast media.
The chute is designed to effectively separate the blast media and collect them in a skip, while the foreign pieces are unloaded to another skip and thus ready to be remelted.
Reduced silica dust emissions
The Superbelt® conveyor provides a competitive edge in dealing with a highly sensitive issue, namely workers' exposure to crystalline silica dust.
The simple operation of the Magaldi conveyor system ensures smooth running without vibrations which, in turn, minimizes dust emissions, contributing to a safer and healthier work environment.
Some successful stories
Italy
Casting degating & sorting
Iron foundry
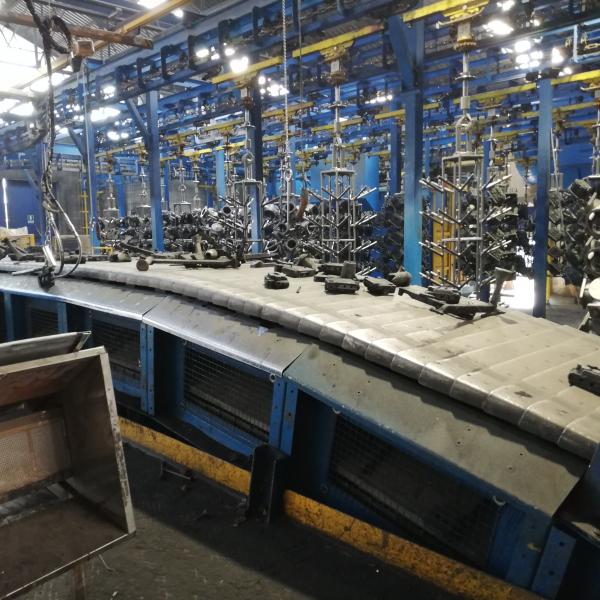
The smooth and gentle transport without vibrations allows keeping dust emissions under control.
The Customer
The foundry produces high-quality grey cast iron pieces weighing from 0.5 to 100 kg per unit.
The Challenge
The existing apron conveyor was extremely high in maintenance and caused many troubles. It was responsible for sand spillage, thus requiring high costs for cleaning. Additionally, this condition did not allow operators to carry out sprue removal and casting sorting operations properly.
The Solution
Downstream the cooling drum, the first section of the Superbelt® conveyor is covered with a hood for dust containment. The second section features a flat surface of the belt and turn-down sidewalls. This special design allows workers to easily and safely sort castings and remove sprues by means of hydraulic wedges.
USA
Casting degating & sorting
Iron foundry
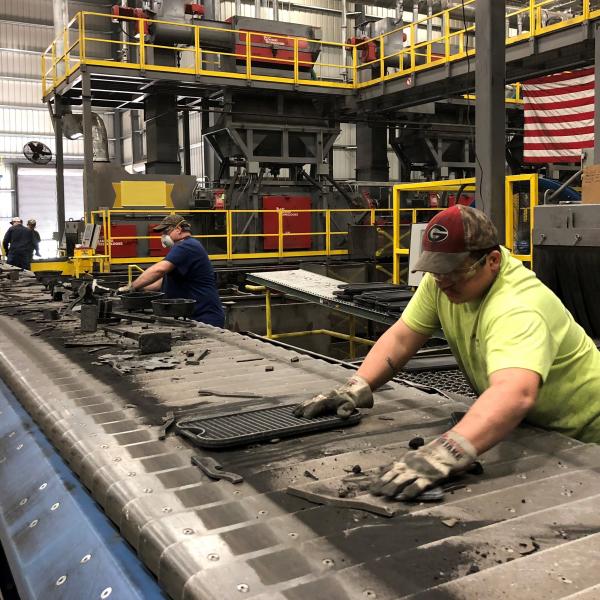
The Superbelt® technology was part of the “recipe” to reduce sand leakage and environmental contamination from silica dust.
The Customer
The oldest and longest-running cast iron cookware manufacturer.
The Challenge
As part of an expansion project to double the plant's capacity, the Customer could not ignore the problem of airborne silica dust control.
The Solution
Magaldi installed 2 Superbelt® conveyors:
- one for casting transportation;
- one for casting sorting and shot-blasting loading.
The Superbelt® technology proved to be a worthy ally for improving both business and working environment by drastically reducing workers' exposure to airborne silica thanks to its smooth and gentle motion without vibrations or shaking.
Czech Republic
Casting degating & sorting
Iron foundry
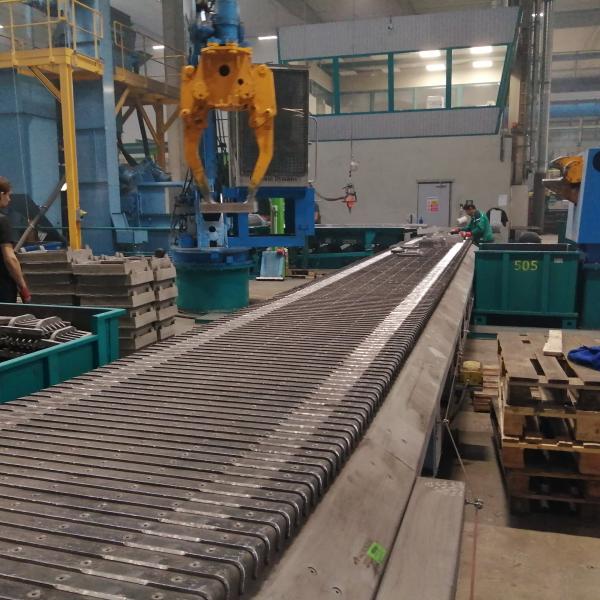
The Superbelt® has been the key factor to contain dust, eliminate spillage, and reduce cleanup costs and time.
The Customer
Leading manufacturer of iron sewage castings, street grilles and other components for the construction industry.
The Challenge
The Customer decided to stop buying from China and India, and start producing castings independently in two new iron foundries. Magaldi was awarded a contract for supplying the cooling system for the second foundry. In the first one, a vibrating system had caused troubles (noise pollution, dust spillage and build-up issues) since the beginning. The Customer was determined not to repeat the same mistake.
The Solution
Magaldi supplied:
- 2 MCC® to cool castings from 600°C to <100°C
- a Superbelt® blast loading conveyor
- a Superbelt® conveyor installed downstream of the shot-blasting process to allow workers to easily sort castings on the steel belt.
Magaldi equipment has proven to be the key factor for a cleaner and safer working environment.